On this page
ToggleDryer Problems Got You Down? Troubleshoot Like a Pro
You’re not alone! Dryer issues are common across brands, from LG and Samsung to Frigidaire and Whirlpool. The good news is many problems can be resolved with simple troubleshooting. Here’s a guide to tackle common dryer dilemmas and get your laundry routine back on track:
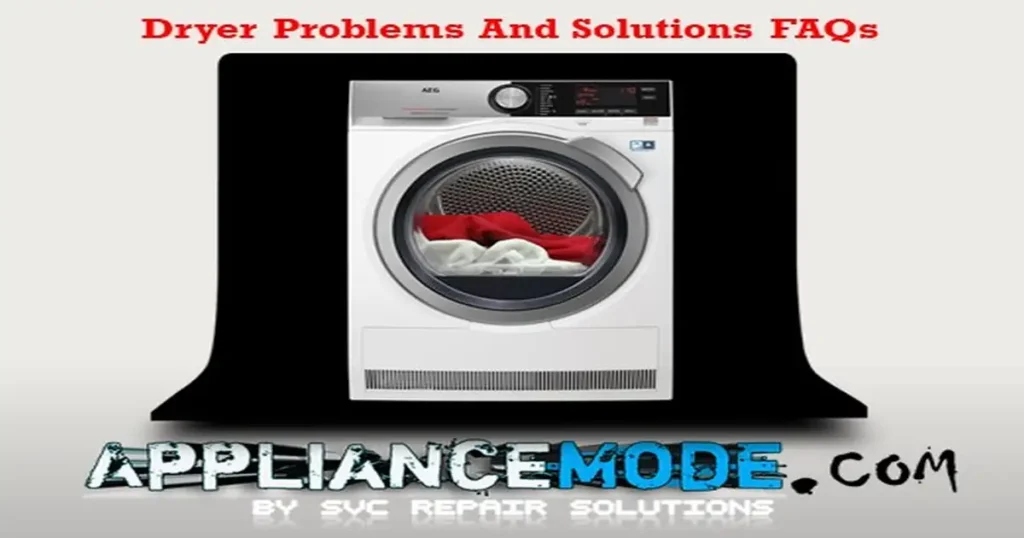
Before You Call a Repair Whiz:
Error Codes Don’t Always Mean Part Replacement: Don’t jump to conclusions when faced with an error code. Check for loose wiring connections first. A simple fix could save you time and money.
Dryer problems and solutions: Diagnostic and Troubleshooting Guide Q&A
The customer experience (CX) may encounter a non-functioning dryer display. This could stem from several factors, such as:
- Insufficient power: An undersized power group or overloaded circuit might not provide enough electricity to power the display.
- Faulty connections: A damaged power extension cord or loose connections within the dryer can disrupt power flow.
- Excessive power draw: Other appliances sharing the same circuit could overload it and limit power to the dryer display.
- Internal malfunction: A short circuit within the dryer or a faulty main board could directly affect the display functionality.
If the CX observes water around or at the dryer, this could be due to several reasons, including an unleveled dryer, condensed water due to placement in a cold environment, a full water tank, leakages in the drain hose, around the door, around the condenser cover, or inside the dryer.
To solve the problem, the customer should check the surrounding temperature and level of the dryer and ensure that the standpipe height does not exceed 1 meter. They should also check for a kinked or restricted drain hose, empty the water tank, and inspect the door, condenser duct, drain connection path, back cover, and dryer base for damage or oxidation.
Customers may report a newly-present, unpleasant odor emanating from their dryer. This issue can arise from several causes, including:
- Wet clothes remaining in the drum for extended periods: Moisture trapped within the dryer can foster mildew growth, leading to a musty or rotten smell.
- Unleveled dryer: An unevenly positioned dryer may hinder proper drainage, contributing to moisture buildup and odor.
- Clogged drain pipe or faulty drain pump: Impaired drainage can trap water within the dryer, fostering odor-causing bacteria and mildew.
- Condensers or ducts clogged with wet lint: Lint accumulation can obstruct airflow and trap moisture, promoting mold and mildew growth.
- To address this problem, guide customers through the following steps:
Prevent moisture buildup:
- Promptly remove clothes upon cycle completion.
- Leave the dryer door open between cycles to promote ventilation.
- Initiate drying cycles within the timeframe specified by the ‘Time Delay’ option.
Ensure proper drainage.
- Inspect the drain hose for kinks or blockages.
- Thoroughly clean the lint filter after every drying cycle.
Address: Clogged Condenser or Ducts:
- Disconnect the dryer from power and carefully inspect the condenser and ducts for wet lint buildup.
- Meticulously remove any lint residue.
Run a High-Heat Cycle (Empty Drum):
- Advise customers to initiate a drying program with an empty drum at the highest temperature setting. This process can aid in eliminating residual moisture and odors.
Inspect the Drain Pump and Dryer Base (If Needed):
- If the odor persists after the aforementioned steps, further inspection of the drain pump and dryer base may be necessary.
If the CX observes a burning odor that was not present before, this could be due to friction between the drum and slider or felt packing, an overloaded motor, new electronics, or overheated parts.
To solve the problem, the customer should check if laundry has been caught between the drum and front seat and if electronic assemblies have been recently installed. They should also inspect the power connections and assemblies, ensure that the connectors on the assemblies are fully inserted, and check the belt and/or motor, ventilator, and drum ball bearings.
When the dryer starts, the display lights up and a program can be selected, but the drum does not rotate. This can be caused by an overloaded dryer, a broken belt driving the drum, damaged bearings, a faulty thermostat, capacitor, motor, or main board.
To solve this issue, start by checking if the dryer was overloaded and removing some clothing. Next, pause the program, open the door, and re-check if the light works. Try rotating the drum and ensuring it rolls with normal force. If you hear an abnormal noise, check the bearings. Also, check the belt, thermostat, capacitor, drum ball bearing, motor and ventilator bearings, and the main PCB.
When laundry is still wet after the drying cycle, it could be because the program was stopped or paused before the end, the wrong drying level was selected, the water tank is full, the dryer was overloaded, the air flow is blocked, the dryer is not leveled properly, the drain hose is kinked or clogged, or the moisture sensor, drain pump, heater, or main board is faulty.
To solve this issue, check if the dryer was overloaded and remove some clothing. Untangle and redistribute the load if it’s lumpy. Select the correct drying level for the desired dryness, and let the dryer finish the program. Pull out and empty the water tank, and ensure the dryer is installed correctly with enough ventilation. Check the dryer’s level, airflow path, moisture sensor, and drain pump. Also, check the drain connection path and main board.
When the laundry feels damp after the drying cycle, it could be because the dryer was overloaded, the load size was too small, the program settings were wrong for the load size and fabric type, there was a mixed fabric load, the dryer is not leveled properly, the dryer lint filter is clogged, or the moisture sensor or main board is faulty.
To solve this issue, check if the dryer was overloaded and remove some clothing. Add a few items or use ‘SPEED DRY’ or ‘TIME DRY.’ Check the load size, fabric type, and program settings for optimum performance. Ensure fabric types are sorted correctly and the dryer is level. Clean the dryer condenser, filter, and check for obstructions in the airflow path. Also, check the moisture sensor and main board.
If the program is taking a long time to end and is stuck for 9–12 minutes, it could be because the dryer is overloaded, the load is still wet, the moisture sensor is faulty, or the main board is faulty.
To solve this issue, wait a short moment to check if the dryer finishes after the final part of the program, where the moisture level is checked and the load is cooled down. Remove some clothing if the dryer is overloaded. Ensure the customer selects the highest possible spin speed for the fabric that was washed. Check the moisture sensor and main board.
If the dryer makes an abnormal hitting or scraping noise, it could be because of loose items in the drum, objects stuck at the front seat, damaged bearings, or a damaged slider and felt packing.
To solve this issue, check the load and remove loose items like zippers, metal buckles, or coins. Ensure snaps and zippers are not on the outside, and use a special washing bag for underwired bras. Check if the laundry has been caught between the drum and the front seat. Rotate the drum and verify it can roll with normal force.
- If you hear an abnormal noise, also:
- Check the bearing.
- Check the slider and felt packing on the front and back.
- Check the motor and ventilator bearings.
- Check the drum ball bearing.
The CX hears an abnormal noise that sounds like thumping. This could be caused by several factors, such as an unleveled dryer, tangled laundry, dented support rollers, or deformation of the drum.
- What steps can be taken to solve the problem?
- To solve the issue, the customer can take several steps, including checking the level of the dryer and ensuring proper contact with the floor. They can also wait a few minutes for the rubber of the support rollers to warm up, as support rollers tend to dent slightly when the dryer is not in use for more than two weeks. Additionally, the customer should check if the load is lumped, untangle it, and redistribute it as necessary.
- They should also check the support rollers and the centrifugal correctness of the drum and the tub using the test mode.
- To solve the issue, the customer can take several steps, including checking the level of the dryer and ensuring proper contact with the floor. They can also wait a few minutes for the rubber of the support rollers to warm up, as support rollers tend to dent slightly when the dryer is not in use for more than two weeks. Additionally, the customer should check if the load is lumped, untangle it, and redistribute it as necessary.
The CX observes vibrations in the dryer, either by touching it or hearing the sounds of resonating items. This could be caused by several factors, such as tangled laundry, dented support rollers, an unleveled dryer, insufficient space on one of the sides of the dryer, or deformation of the drum (oval).
- What steps can be taken to solve the problem?
- To solve the issue, the customer can wait a few minutes for the rubber of the support rollers to warm up, as support rollers tend to dent slightly when the dryer is not in use for more than two weeks. They should also check if the load is lumped, untangle it, and redistribute it as necessary, which can also reduce drying time.
- The customer should check if the dryer is touching the wall and ensure there is enough space for proper ventilation. They should also check if the support brackets are attached correctly to the pedestal and the dryer, and finally check the level of the dryer, the support rollers, and the centrifugal correctness of the drum and the tub.
- To solve the issue, the customer can wait a few minutes for the rubber of the support rollers to warm up, as support rollers tend to dent slightly when the dryer is not in use for more than two weeks. They should also check if the load is lumped, untangle it, and redistribute it as necessary, which can also reduce drying time.
The CX observes a too high temperature in the dryer, causing clothing to be very hot or shrink excessively. This could be caused by several factors, such as stopping or pausing the program before the end, blocked airflow, a clogged dryer lint filter, a blocked or damaged condenser, a faulty moisture sensor, a faulty thermostat, a faulty thermistor, or a faulty main board.
- What steps can be taken to solve the problem?
- To solve the issue, the customer can check the load size, fabric type, and program settings for optimum performance, allowing the dryer to finish the program to prevent damage to clothing. They should also clean the dryer filter and condenser and remove any lint and softener residues using warm water.
- The customer should also check if the dryer is installed correctly with enough room for ventilation and check the airflow path for obstructions. Additionally, they should check the moisture sensor, thermostat, thermistor, heater, and main board.
- To solve the issue, the customer can check the load size, fabric type, and program settings for optimum performance, allowing the dryer to finish the program to prevent damage to clothing. They should also clean the dryer filter and condenser and remove any lint and softener residues using warm water.
The ‘Empty Water’ LED is an indicator that the water tank is full and needs to be emptied, with the water flowing back to the base.
- What could be the cause of this problem?
- The issue could be caused by a full water tank, a kinked or clogged drain hose, a faulty drain pump, a faulty drain pump sensor, or a faulty main PCB.
- What steps can be taken to solve the problem?
- To solve the issue, the customer can pull out the water tank and empty it, check for a kinked or restricted drain hose, pipe, or utility sink, and ensure proper drainage. They should also check the drain pump, drain pump sensor, and main PCB.
The ‘Clean Filter’ LED indicates a problem with the warm air flowing through the dryer, which can be caused by various factors such as blocked air flow, a clogged dryer lint filter, a blocked condenser, or a faulty main PCB.
- To solve this issue, the following steps can be taken:
- Unplug the dryer, wait for 60 seconds, and restart the dryer.
- Clean the dryer filter and remove any lint. It is recommended to use warm water to dissolve any softener residues.
- Check the airflow path for any obstructions.
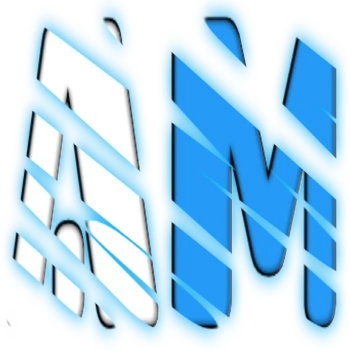
I am a master Appliance Repair technician with over 35 years of experience in the field. I am passionate about helping people troubleshoot their appliances and fix common problems. My website, appliancemode.com, provides a wealth of information on troubleshooting common appliance issues and deciphering error codes. This website aims to empower people to tackle appliance repairs themselves and save money on service calls.