Facing a flashing error code on your Haier washing machine can interrupt your laundry routine and leave you wondering what went wrong. Don’t despair! This guide is designed to help you understand the most common Haier washing machine error codes, offering straightforward troubleshooting techniques and potential DIY fixes for minor issues.
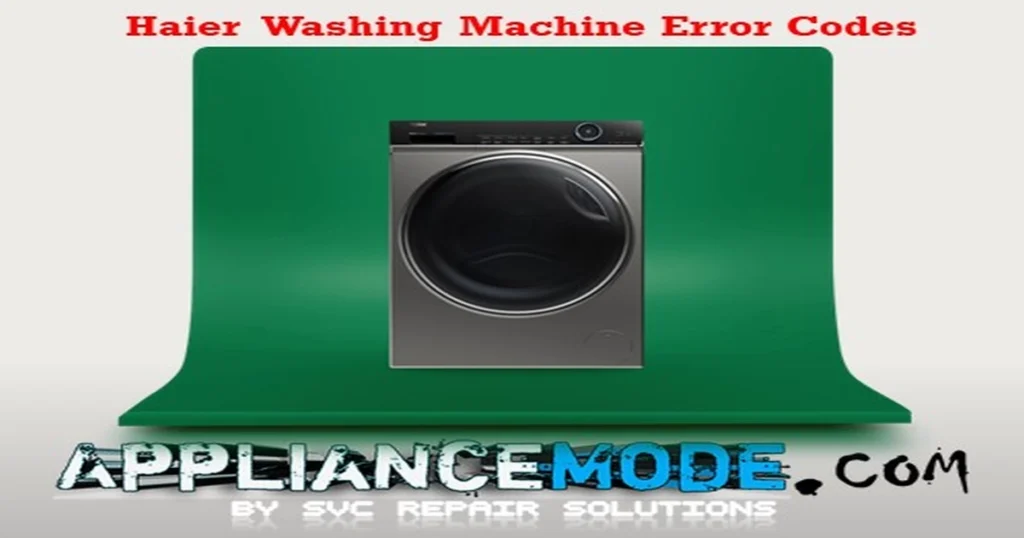
Whether you own a recent model or a trusted older machine, this breakdown will help you diagnose the problem and hopefully get your washing machine back in action.
Here are some of the common Haier washing machine error codes you might encounter:
Important Safety Warning: Always unplug your Haier washing machine from the power outlet before attempting any inspection, cleaning, or repair. Electrical components can be dangerous, and water can pose an electrical hazard. If you are uncomfortable working with electrical parts or complex internal components, it is always best to contact a qualified appliance repair technician.
CLR FLTR (or E1/E12): Drainage Error
What it means: This error indicates that the washing machine is unable to drain the water within the expected time frame, usually around 6 minutes.
Possible Causes:
- A clogged drain filter or drain hose.
- Issues with the drain pump.
- A blocked or kinked pressure switch hose.
- A faulty main control board (PCB).
Troubleshooting & Fixes:
- Check the Drain Filter:
- Locate the drain filter, usually at the bottom front of the machine behind a small panel.
- Place a towel or shallow container underneath to catch any residual water.
- Carefully unscrew and remove the filter.
- Clean the filter thoroughly, removing any lint, coins, or foreign objects.
- Check the filter housing for blockages as well.
- Reinsert and secure the filter.
- Inspect the Drain Hose:
- Ensure the drain hose is not kinked, bent, or blocked along its length.
- Verify that the drain hose is not inserted too far into the standpipe (the vertical drain pipe) – typically, only about 4-6 inches is needed.
- Check if the standpipe itself is clogged. You can test this by pouring a bucket of water down the pipe.
- Check the Pressure Switch Hose:
- Locate the pressure switch and the small, thin hose connected to it (it usually runs down to the drum).
- Ensure this hose is not kinked or blocked. A blockage here can trick the machine into thinking there’s still water when there isn’t, or vice versa.
- Carefully disconnect the hose at both ends and check for obstructions by blowing through it (ensure the other end is not submerged in water).
- Check Drain Pump Connection and Resistance:
- (Requires comfort with electrical components and a multimeter)
- Locate the drain pump.
- Check the wire connection between the drain pump and the main control board (Power PCB). Ensure it is secure.
- If you have a multimeter, you can check the resistance of the drain pump. Refer to your machine’s manual for the exact location of the pump and the correct terminals to test.
- Typical Ohmic Value: Drain pump: ~224 Ω (Note: This value can vary slightly by model. Use the value provided in your service manual if available).
- If the resistance reading is significantly different or open circuit, the drain pump may be faulty and require replacement.
- Faulty Main PCB: If the above steps do not resolve the issue, the problem might be with the main control board, which would require professional diagnosis and repair.
E2: Door Lock Failure
What it means: The washing machine’s electronic board is not receiving a signal that confirms the door is securely closed and locked, preventing the cycle from starting.
Possible Causes:
- The washer door is not closed properly.
- Laundry is caught between the door and the door frame.
- A faulty door lock mechanism.
- A problem with the wiring between the door lock and the main control board.
- A faulty main control board (PCB).
Troubleshooting & Fixes:
- Ensure the Door is Fully Closed: Open and firmly close the washing machine door, ensuring you hear a distinct click as it latches.
- Check for Obstructions: Make sure no clothing items or other objects are trapped between the door and the drum seal.
- Check Wire Connection to Door Lock:
- (Requires comfort with electrical components and unplugging the machine)
- Locate the door lock assembly.
- Check the wire connection between the door lock and the main control board (Power PCB). Ensure it is secure.
- Check Door Lock Resistance:
- (Requires comfort with electrical components and a multimeter)
- With the machine unplugged, you can test the resistance of the door lock mechanism using a multimeter.
- Typical Ohmic Value: Door lock: ~198 Ω (Note: This value can vary slightly by model. Use the value provided in your user manual if available).
- If the resistance is significantly off or indicates an open circuit, the door lock is likely faulty and needs to be replaced.
- Faulty Main PCB: If the door lock appears to be functioning correctly and the wiring is secure, the issue might stem from the main control board, requiring professional attention.
F3: Water Temperature Sensor Failure (NTC)
What it means: There is an issue with the sensor that measures the water temperature inside the drum (the NTC thermistor). The control board isn’t receiving accurate temperature information.
Possible Causes:
- A faulty wire connection to the NTC sensor.
- A faulty NTC temperature sensor itself.
- A faulty main control board (PCB).
Troubleshooting & Fixes:
- Check Wire Connection to NTC:
- (Requires comfort with electrical components and unplugging the machine)
- Locate the NTC sensor, which is usually located near the heating element.
- Check the wire connection between the NTC and the main control board (Power PCB). Ensure it is secure.
- Check NTC Sensor Resistance:
- (Requires comfort with electrical components and a multimeter)
- With the machine unplugged, disconnect the NTC sensor and measure its resistance using a multimeter. The resistance of the NTC changes with temperature.
- Typical Ohmic Value: NTC sensor at 30 °C: ~9.788 KΩ (Note: This value is temperature-dependent and can vary slightly by model). You can test the resistance at room temperature and compare it to the expected value for that temperature (often found in the service manual).
- If the resistance reading is significantly outside the expected range, the NTC sensor is likely faulty and needs replacement.
- Faulty Main PCB: If the NTC sensor and its wiring appear to be in good condition, the issue may lie with the main control board, requiring professional diagnosis.
E4: Water Inlet Error
What it means: The washing machine is not filling with enough water, or not filling within the allocated time (usually 8 minutes) during the water intake phase.
Possible Causes:
- The water tap is turned off or the water pressure is too low.
- A clogged filter screen in the water inlet valve.
- A faulty water inlet valve.
- A damaged harness connection to the inlet valve or pressure switch.
- A leaky pressure sensor hose or a clogged air chamber.
- Frozen water supply pipes (in cold weather).
- A faulty main control board (PCB).
- The drain hose is siphoning water out as it fills (the drain hose height is too low).
Troubleshooting & Fixes:
- Check Water Supply:
- Ensure both the hot and cold water taps connected to the washing machine are fully turned on.
- Verify that you have adequate water pressure in your home by checking other taps.
- Clean Water Inlet Valve Filter Screen:
- Turn off the water taps connected to the machine.
- Disconnect the fill hoses from the back of the washing machine.
- Inside the water inlet ports on the machine, you will see small filter screens.
- Carefully remove these screens (pliers may be needed) and clean them under running water with a small brush to remove sediment or debris.
- Reinsert the filters and reconnect the hoses, ensuring they are hand-tightened securely (do not overtighten).
- Check Drain Hose Height: Ensure the drain hose is installed at the correct height, typically between 80 cm and 100 cm from the floor. If it’s too low, water can continuously drain out as the machine attempts to fill.
- Check Pressure Switch Hose and Air Chamber:
- Locate the pressure switch and its hose.
- Check the hose for any leaks or kinks.
- Inspect the air chamber (where the pressure hose connects to the drum) for blockages.
- Check Inlet Valve Resistance:
- (Requires comfort with electrical components and a multimeter)
- With the machine unplugged and water taps off, locate the water inlet valve(s) at the back of the machine.
- Disconnect the electrical connectors to the valve(s).
- Measure the resistance across the terminals of each solenoid valve using a multimeter.
- Typical Ohmic Value: Inlet valve: ~4 KΩ (Note: This value can vary slightly by model).
- If the resistance is significantly different, the inlet valve may be faulty and require replacement.
- Check Harness Connections: Inspect the wiring harness connections to the water inlet valve and the pressure switch for any damage or loose connections.
- Frozen Pipes: In cold climates, ensure your water supply pipes are not frozen.
- Faulty Main PCB: If none of the above steps resolve the E4 error, the main control board may be the culprit, requiring professional diagnosis and repair.
F4: Heater Error
What it means: The washing machine is detecting an issue with the water heating system. The water temperature is not increasing as expected during a heating cycle.
Possible Causes:
- A faulty wire connection to the heating element.
- A faulty heating element assembly.
- A faulty temperature sensor (NTC) – although this often triggers an F3 code, it can sometimes contribute to F4.
- A faulty main control board (PCB).
Troubleshooting & Fixes:
- Check Wire Connection to Heater:
- (Requires comfort with electrical components and unplugging the machine)
- Locate the heating element, usually at the bottom of the drum.
- Check the wire connection between the heater and the main control board (Power PCB). Ensure it is secure.
- Check Heater Assembly Resistance:
- (Requires comfort with electrical components and a multimeter)
- With the machine unplugged, locate the heating element.
- Disconnect the electrical connectors to the heater.
- Measure the resistance across the heater terminals using a multimeter.
- Typical Ohmic Value: Heater assembly: ~30 Ω (Note: This value can vary slightly based on the heater’s wattage and model).
- If the resistance is significantly different (e.g., open circuit), the heating element is likely faulty and needs to be replaced.
- Check for Voltage to Heater:
- (Requires caution with live electrical components and a multimeter)
- This step should only be performed by someone comfortable and knowledgeable about working with live electricity.
- With the machine in a heating cycle (exercise extreme caution as components are live), check if there is the rated input voltage across the heater terminals.
- If there is voltage but the heater is not heating and its resistance was correct, the heater might still be faulty internally, or there’s an issue with the NTC sensor (F3).
- If there is no voltage to the heater, the problem is likely with the main control board.
- Faulty Main PCB: If the heating element appears functional and the wiring is secure, the main control board may be faulty, requiring professional repair.
F7: Motor Error
What it means: There is a problem with the washing machine’s motor or the system that controls and monitors the motor’s rotation. The machine cannot accurately detect or control the motor speed.
Possible Causes:
- A faulty wire connection to the motor or the motor control board (driven board/inverter board).
- A faulty motor (Direct Drive – DD motor or BLDC motor depending on the model).
- A faulty tachometer (a sensor that measures motor speed, often integrated into the motor).
- A faulty inverter board (for inverter models).
- A faulty main control board (PCB).
Troubleshooting & Fixes:
- Check Wire Connections:
- (Requires comfort with electrical components and unplugging the machine)
- Locate the motor and the motor control board (driven board or inverter board, often near the motor).
- Check the wire connections between the main control board, the motor control board, and the motor itself. Ensure all connections are secure.
- Check Motor Resistance:
- (Requires comfort with electrical components and a multimeter)
- With the machine unplugged, disconnect the motor’s electrical connector.
- Measure the resistance of the motor windings using a multimeter.
- Typical Ohmic Values:
- DD MOTOR 8KG: ~14.2 Ω
- DD MOTOR 9KG & 10KG: ~27.5 Ω
- BLDC MOTOR: ~6.3 Ω
- (Note: These values can vary by model. Refer to your user manual or service manual if available).
- If the resistance readings are significantly different or indicate an open circuit, the motor may be faulty and require replacement.
- Check Tachometer (Non-Inverter Models):
- For older, non-inverter models, the F7 error often relates to the tachometer. Locate the tachometer wires on the motor and check their connection and potentially the tachometer’s resistance or voltage output (refer to a service manual for specific testing procedures).
- Check Inverter Board (Inverter Models):
- For inverter models, the F7 error can indicate an issue with the inverter board. Some inverter boards have an LED indicator that can provide diagnostic information (e.g., flashing lights might indicate an error). Check the LED status as described in your manual or the blog post’s original text (LED off/flashing/on all suggest different potential issues).
- If the inverter board is suspected, professional diagnosis is recommended as these components are complex and costly.
- Faulty Main PCB: If the motor, wiring, and inverter board (if applicable) appear functional, the issue might be with the main control board, requiring professional repair.
E8: Water Exceeds the Protective Level
What it means: The washing machine’s pressure switch or water level sensor detects that the water level in the drum has risen above a safe, predetermined limit, triggering an overflow protection mechanism.
Possible Causes:
- A faulty water inlet valve that is not closing properly, allowing water to continuously fill.
- A problem with the pressure sensor or water level sensor.
- A clogged or leaky pressure sensor hose or a clogged air chamber, leading to inaccurate water level readings.
- A damaged wiring harness to the water inlet valve or pressure sensor.
- A faulty main control board (PCB).
Troubleshooting & Fixes:
- Observe Water Filling: If water continues to fill even when the machine is off or after the E8 error appears, the water inlet valve is likely faulty and not closing correctly. Turn off the water supply immediately and replace the inlet valve.
- Check Pressure Sensor Hose and Air Chamber:
- Locate the pressure sensor and its hose.
- Check the hose for any leaks or kinks. A pinhole leak can cause the pressure to drop, leading to an overfill.
- Inspect the air chamber (where the pressure hose connects to the drum) for blockages. Remove any foreign material.
- Check Water Level Sensor:
- If the water level appears normal but the E8 error is displayed, the water level sensor itself might be faulty.
- (Requires comfort with electrical components and potential part replacement)
- Check the wire connection to the water level sensor.
- If comfortable, you may attempt to replace the water level sensor.
- Check Wiring Harness: Inspect the wiring harness connected to the water inlet valve and the pressure sensor for any signs of damage or loose connections.
- Faulty Main PCB: If the water inlet valve is not the issue and the pressure sensing system appears functional, the problem could be with the main control board, requiring professional diagnosis. Short circuits on the AC line switch for the water valve on the main board can cause continuous filling and the E8 error.
FA: Water Level Sensor Error
What it means: The washing machine’s control system is not receiving a valid signal from the water level sensor (pressure sensor), making it unable to accurately determine the water level in the drum.
Possible Causes:
- A damaged wiring harness to the water level sensor or display board.
- A leaky pressure sensor hose or a clogged pressure chamber, leading to inaccurate readings.
- A faulty water level sensor (pressure sensor).
- A faulty display control board.
Troubleshooting & Fixes:
- Check Wire Connections:
- (Requires comfort with electrical components and unplugging the machine)
- Check the wire connection between the water level sensor and both the main control board and potentially the display control board (depending on the model’s wiring). Ensure connections are secure.
- Check Pressure Sensor Hose and Pressure Chamber:
- Inspect the pressure sensor hose for any leaks or kinks.
- Check the pressure chamber (where the hose connects to the drum) for blockages.
- Replace Water Level Sensor: If the hose and chamber are clear and the wiring is secure, the water level sensor itself is likely faulty and needs to be replaced.
- Replace Display PCB: In some models, a communication issue with the display board can trigger an FA error. If replacing the water level sensor doesn’t fix the issue, and wiring is confirmed good, the display PCB might be faulty.
FC0, FC1, FC2: Communication Errors
What it means: These codes indicate a failure in communication between different electronic control boards within the washing machine.
- FC0: Communication error between the main control board and the user interface (display board).
- FC1: Communication error between the main control board (PCB) and the inverter board (motor control board).
- FC2: Communication error between the display board and the power board (main PCB). (Note: This seems similar to FC0 and might be a model-specific variation).
Possible Causes:
- A damaged or loose wiring harness connection between the affected control boards.
- A short circuit or open circuit in the wiring.
- A faulty display board.
- A faulty inverter board (for FC1).
- A faulty main control board (PCB).
Troubleshooting & Fixes:
- Check Wire Connections:
- (Requires comfort with electrical components and unplugging the machine)
- Locate the main control board, display board, and inverter board (if applicable).
- Check all wiring connections between these boards. Ensure they are firmly inserted and that there are no signs of damage, such as pinched or cut wires, or burnt connectors.
- Look for potential short circuits or open circuits in the harness.
- Check Inverter Board LED Indicator (for FC1): As mentioned in the original text, check the status of the LED indicator on the inverter board if present. Its state (off, flashing, on) can provide clues about the inverter board’s status or power supply.
- Replace Suspected Control Board: If wiring appears intact and secure, the issue is likely with one of the control boards. Replacing control boards is often a process of elimination and can be costly.
- For FC0/FC2, the display board or main PCB could be at fault.
- For FC1, the inverter board or main PCB could be at fault.
- Professional diagnosis is strongly recommended for these errors as replacing the wrong board can be expensive and won’t solve the problem.
UNB: Unbalanced Load Error
What it means: The washing machine has detected excessive vibration or an uneven distribution of laundry inside the drum during the spin cycle. This is a safety feature to prevent damage to the machine.
Possible Causes:
- Laundry is clumped together on one side of the drum.
- The machine is overloaded with too many items.
- Washing a single large, heavy item (like a blanket or rug) by itself.
- The washing machine is not level.
- Worn suspension parts (shock absorbers or springs).
Troubleshooting & Fixes:
- Redistribute the Load:
- Stop the wash cycle.
- Open the washing machine door.
- Manually rearrange the laundry inside the drum to distribute the weight evenly.
- If the machine is overloaded, remove some items and try spinning a smaller load.
- Add More Items to Small Loads: Sometimes, a very small load, especially of bulky items, can become unbalanced. Adding a few towels can help balance the load.
- Check Machine Level: Use a spirit level to ensure the washing machine is standing perfectly flat on the floor. Adjust the leveling feet at the bottom of the machine as needed.
- Ensure Transit Bolts are Removed: If your machine is new or has been moved, double-check that the transit bolts (used to secure the drum during transport) have been completely removed from the back of the machine.
- Consider Worn Suspension Parts: If unbalanced loads are a recurring problem despite proper loading and leveling, the internal suspension components (like shock absorbers or springs) may be worn and require professional inspection and replacement.
Additional Tips for Preventing Unbalanced Loads:
- Wash heavy items separately from lighter items.
- Avoid washing a single large item alone; add other items to help balance.
- Use the appropriate spin speed for the type of laundry being washed.
clot or clol-: Child Lock or Control Lock Notification
What it means: This is not an error code indicating a fault, but rather a notification that the Child Lock or Control Lock feature is activated. This feature prevents buttons from being pressed and settings from being changed, usually to avoid accidental operation by children or during cleaning.
Causes:
- The Child Lock or Control Lock feature has been intentionally or accidentally activated.
Solutions:
- Deactivate the Lock: The method to deactivate the lock can vary slightly by model, but a common method for Haier machines is to press and hold a specific combination of buttons for a few seconds (often indicated by an icon on the control panel). The original text suggests pressing and holding the “Delay” and “Steam” buttons for 3 seconds.
- Refer to Your User Manual: For the most accurate instructions on how to activate and deactivate the child lock on your specific Haier model, always consult your washing machine’s user manual.
General Troubleshooting Tips (No Specific Code Displayed)
If your Haier washing machine is not starting or functioning correctly but isn’t displaying an error code, consider these general troubleshooting steps:
- Check the Power Supply: Ensure the machine is plugged in securely and that the power outlet is working (you can test it with another appliance). Check your home’s circuit breaker or fuse box for tripped breakers or blown fuses.
- Check the Water Supply: Make sure the water taps are on and that the fill hoses are not kinked.
- Ensure the Door is Closed: Double-check that the door is fully closed and latched.
- Cycle is Selected: Ensure a wash cycle has been properly selected.
- Press Start: Make sure you have pressed the “Start” button.
- Reset the Machine: Sometimes, simply unplugging the machine for a few minutes (e.g., 5-10 minutes) can reset the electronic controls and resolve temporary glitches.
While some Haier washing machine errors can be resolved with simple checks and DIY fixes, others indicate more complex internal issues. Always prioritize safety by unplugging the machine before inspecting components.
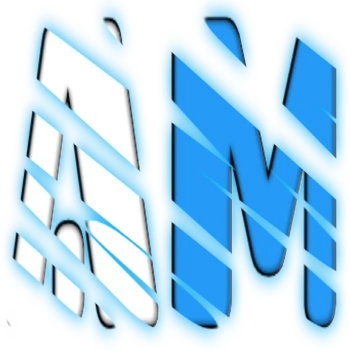
I am a master Appliance Repair technician with over 35 years of experience in the field. I am passionate about helping people troubleshoot their appliances and fix common problems. My website, appliancemode.com, provides a wealth of information on troubleshooting common appliance issues and deciphering error codes. This website aims to empower people to tackle appliance repairs themselves and save money on service calls.
I am facing error “FF ” blinking at washer model HMW200-M1990DD….. when I check didn’t have in error list…
I am facing issue of water drainage without stoppage resulting E4 error even water inlet is correct.water is coming through inlet and immediately draining what can be the issue
I am facing issue of when i start wm no one button can work even starting error fc0.
My washing Machine fco alarm come please solve my washing machine problem tell me