Hisense washing machines are equipped with an error code mode to assist homeowners and/or technicians in troubleshooting and resolving issues. In this article, we will explore the Hisense washing machine error codes, providing you with the knowledge to effectively address any problems that may arise.
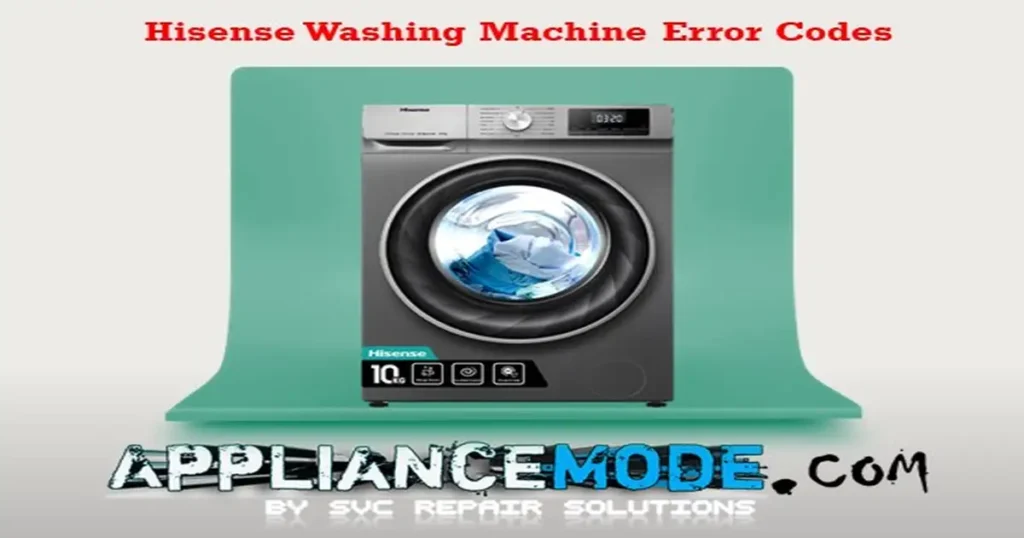
Let’s dive in and discover the key to understanding these error codes!
Hisense washing machine error codes explained: Troubleshooting Made Easy
Remember to always unplug the washer and exercise caution when attempting any repairs.
F01: Water Inlet Error
The F01 error code indicates that the correct water level has not been reached within 4 minutes. This issue could arise due to various reasons related to water inlet functionality.
Solutions:
- Ensure that the water pressure in your house is sufficient for proper water to flow into the washing machine.
- Clean the filter to remove any foreign material that may be obstructing the water flow.
- Ensure the drain hose is positioned no more or less than 60 cm above the bottom of the washing machine. This prevents water from backflowing and causing issues with the water inlet.
- Inspect the wiring connections between the water inlet valve and the main board for any loose or damaged wires.
- Measure the resistance between each terminal of the inlet valve. The resistance should read between 3.80 and 4 KΩ. If not, replace the inlet valve.
Electric part name | Ohmic value | Abnormal value |
---|---|---|
Water inlet valve | 0.9 KΩ @ 120 Vac | 4 KΩ @ 220 Vac | 0.1 – 1.2 Ω | OL |
- If the error persists despite the above steps, consider replacing the main board, as it could be the source of the issue.
F03: Drainage Error
The F03 error code indicates that the washing machine has not been fully drained within 6 minutes. This issue could be related to problems with the drain system.
Solutions:
- Inspect the drain filter and clean it to remove any debris or obstructions that may be impeding the water flow.
- Ensure the drainage hose is not bent or clogged. Straighten any bends and clear any blockages to allow smooth water drainage.
- Check the wiring connections between the drain pump and the main board for any loose or damaged wires.
- Measure the resistance of the drain pump coil. The resistance should range between 160 and 198 ohms. If it falls outside this range, replace the drain pump.
Electric part name | Ohmic value | Abnormal value |
---|---|---|
Drain pump | ~ 16 Ω @ 120 Vac | ~ 198 Ω @ 220 Vac | 0.1 – 1.2 Ω | OL |
- If the error persists despite performing the above steps, consider replacing the main board, as it could be the cause of the drain error.
F04: Heating Error
The F04 error code indicates that the heater in the washing machine is malfunctioning. This issue can prevent the water from reaching the desired temperature during the wash cycle.
Solutions:
- Inspect the wiring connections between the heater and the main board for any loose or damaged wires. Ensure that the connections are secure and properly connected.
- Measure the resistance of the heater. The resistance should fall between 26 and 30 Ω. If the resistance is outside this range, it indicates a faulty heater, and it should be replaced.
Electric part name | Ohmic value | Abnormal value |
---|---|---|
Heater assembly | ~ 18 Ω @ 120 Vac | ~ 30 Ω @ 220 Vac | 0.1 – 1.2 Ω | OL |
- If the error persists despite performing the above steps, consider replacing the main board, as it could be the cause of the heating error.
F05: Water Temperature Sensor Error
The F05 error code occurs when the water temperature sensor (NTC) value is outside the acceptable range during the water heating phase of the wash cycle. This indicates a problem with the sensor’s readings.
Solutions:
- Inspect the wiring connections between the temperature sensor and the main board. Ensure that there are no loose or damaged wires and that the connections are securely in place.
- Measure the resistance of the temperature sensor. At a temperature of 30°C, the resistance should be around 9.7 KΩ. If the resistance deviates significantly from this value, it indicates a faulty sensor, and it should be replaced.
Electric part name | Ohmic value | Tempurature |
---|---|---|
Water temperature sensor | ~ 9.7 KΩ | 30°C | 86°F |
- If the error persists even after following the above steps, consider replacing the main board, as it could be the cause of the water temperature sensor error.
F06: Motor Tachometer Error
The F06 error code occurs when the control system fails to accurately detect the motor speed multiple times, leading to a shutdown of the washing machine.
Solutions:
- Inspect the wiring connections between the motor assembly and the main board. Ensure that all wires are properly connected and that there are no loose or damaged connections.
- Measure the resistance of the tachometer. The expected resistance value should be around 103 Ω. If the resistance deviates significantly from this value, it indicates a faulty tachometer, and the motor may need to be replaced.
Electric part name | Ohmic value | Abnormal value |
---|---|---|
Tachometer | ~ 103 Ω | 0.1 – 1.2 Ω | OL |
- Verify the motor’s resistance using the specified table values. If the resistance falls outside the acceptable range, it suggests a faulty motor that should be replaced.
Electric part name | Ohmic value | Abnormal value |
---|---|---|
Motor rotor | ~ 1.9 Ω | 0.01 Ω | OL |
Motor stator, low speed | ~ 0.8 Ω | 0.01 Ω | OL |
Motor stator, full speed | ~ 2.2 Ω | 0.01 Ω | OL |
- If the error persists despite performing the above steps, consider replacing the main board, as it could be the cause of the motor tachometer error.
F07: Motor Control TRIAC Error
The F07 error code indicates that the main board system has detected a short circuit in the motor TRIAC.
Solutions:
- Check the resistance of the tachometer using a multimeter. The expected resistance value should be around 103 Ω. If the resistance measurement shows a shorted or open circuit, it indicates a faulty tachometer. In such cases, the motor may need to be replaced.
- If the error persists despite following the above steps, consider replacing the main board. The main board could be the cause of the motor control TRIAC error, and replacing it may resolve the issue.
F08: Motor Inverter Error
The Hisense washing machine F08 error code indicates an issue with the motor inverter. This motor is responsible for rotating the drum during wash and spin cycles. When the inverter control board detects a problem with this motor, it displays the F08 error.
Here’s a breakdown of the potential causes and solutions:
Possible Causes:
- Faulty Inverter Motor: The motor itself might be defective due to worn-out components, internal damage, or electrical issues.
- Wiring Problems: Loose connections, damaged wires, or corrosion in the wiring harness connecting the motor to the control board can disrupt communication and trigger the error.
- Motor inverter or Control Board Malfunction: A problem with the main control board, which regulates the motor’s operation, can also lead to the F08 error.
- Motor Overload: Excessive load in the drum or an obstruction preventing it from rotating freely can strain the motor and cause the error.
Troubleshooting and Solutions:
- Check for Overload: Ensure the washing machine isn’t overloaded with laundry. Remove some items if necessary and try running a cycle again.
- Inspect Wiring: Carefully examine the wiring connections to the inverter motor and the control board. Look for any loose connections, frayed wires, or signs of corrosion. Reconnect any loose wires and repair or replace damaged ones.
- Reset the Machine: Turn off the washing machine and unplug it from the power outlet for a few minutes. Then, plug it back in and try running a cycle. This might reset the control board and clear the error.
- Check for Obstructions: Make sure there are no obstructions preventing the drum from rotating freely. Check for items caught between the drum and the outer tub.
- If the above steps don’t resolve the issue, replace the inverter motor, or the inverter control board if necessary.
F13: Door Look Error “Door Open LED flashing after the cycle is started.”
The F13 error code occurs when the door is not fully closed while the cycle has been initiated.
Solutions:
- Ensure that the door is fully closed and latched securely. Sometimes, a partially closed or improperly latched door can trigger the F13 error.
- Inspect the door lock mechanism to ensure there are no obstructions or malfunctions preventing proper locking of the door.
- Check the wiring connections between the main board and the door lock. Look for any loose or damaged wires that may be causing a faulty connection.
- Measure the resistance of the door lock between pin 3 and pin 5. The expected resistance value should be around 900 Ω. If the resistance deviates significantly from this value, it indicates a faulty door lock that may need to be replaced.
Electric part name | Ohmic value | Abnormal value |
---|---|---|
Door lock | ~ 900 Ω | 0.1 – 1.2 Ω | OL |
- If the error persists despite following the above steps, consider replacing the main board, as it could be the cause of the F13 error.
F15: Outlet Dry Air Temperature Sensor Error
The F15 error code occurs when the Outlet Dry Temperature Sensor (NTC) value is outside the acceptable range during the drying cycle. This indicates a problem with the sensor’s readings.
Related error code:
F16: Return Dry Air Temperature Sensor Failure:
- The F16 error code occurs when the Return Dry Air Temperature Sensor (NTC) value is outside the acceptable range during the drying cycle. This also indicates a problem with the sensor’s readings.
Solutions:
- Check the wiring connections between the drying temperature sensor and the main board. Ensure that all wires are securely connected and that there are no loose or damaged connections that could affect the sensor’s readings.
- Measure the resistance of the drying temperature sensor using the specified table values. At a temperature of 40°C, the resistance should be around 6.8 KΩ. If the resistance is outside of this value, it indicates a faulty sensor that should be replaced.
Electric part name | Ohmic value | Tempurature |
---|---|---|
Outlet Dry Air Temperature Sensor | ~ 6.8 KΩ | 40°C | 104°F |
Return Dry Air Temperature Sensor | ~ 6.8 KΩ | 40°C | 104°F |
- If the error persists despite performing the above steps, consider replacing the main board, as it could be the cause of the temperature sensor fault alarm.
F17: Drying Overheating Error
The F17 error code indicates a drying overheating error. This means that during the drying process, the temperature has exceeded safe limits, potentially leading to an F17 error.
Solutions:
- Overloading the machine can cause it to work harder and generate excessive heat. Try reducing the load size to allow for better airflow and heat dissipation.
- Double-check the selected drying settings to ensure that they are appropriate for the fabric type and load size. Using high heat settings unnecessarily can contribute to overheating.
- If the machine has overheated, it’s important to let it cool down for approximately 45 minutes before resuming operation. This allows the internal components to return to a safe temperature.
- If the washing machine is located in a space with high ambient temperatures, it can impact the drying process and lead to overheating. Ensure proper ventilation or consider relocating the machine to a cooler area if possible.
- Check the drying temperature sensor.
F18: Drying Fan Error
The F18 error code indicates a drying fan error. This means that during the drying cycle, the fan has failed to function properly, resulting in an F18 error.
Solutions:
- Inspect the wiring connections between the drying fan and the main board. Ensure that all wires are securely connected and that there are no loose or damaged connections that could affect the fan’s operation.
- Check the drying turbine set to ensure that it is properly installed and functioning correctly. Pay particular attention to the fan blade for any signs of damage or obstruction that may hinder its rotation.
- Measure the resistance of the fan phases using a multimeter. The expected resistance value should be around 5 Ω. If the resistance is outside of this value, it indicates a faulty fan that may need to be replaced.
- If the error persists despite performing the above steps, consider replacing the main board, as it could be the underlying cause of the drying fan error.
F22: Motor Communication Failure
The F22 error code indicates a motor communication failure. This means that there are malfunctions or communication issues between the inverter board, main board, and motor, resulting in the error.
Solutions:
- Inspect the wiring connections between the inverter board and the main board. Ensure that all wires are securely connected and that there are no loose or damaged connections that could disrupt the communication between the two boards.
- Check the wiring connections between the inverter board and the motor. Verify that all wires are properly connected and that there are no loose or damaged connections that could interfere with the communication between the inverter board and the motor.
- If the error still occurs despite checking the wiring harnesses, consider replacing the inverter board. A faulty inverter board can hinder communication between the main board and the motor, leading to an error code.
- If the error still persists even after replacing the inverter board, consider replacing the main board. The main board may be the cause of the motor communication failure, and replacing it can resolve the issue.
F23: Pressure Sensor Error
The F23 error code indicates a pressure sensor error. This means that there is an issue with the pressure sensor, which is responsible for detecting and measuring the water level in the appliance.
Solutions:
- Inspect the wiring connections between the pressure sensor and the main board. Ensure that all wires are securely connected and that there are no loose or damaged connections that could disrupt the signal between the sensor and the main board.
- Check the air chamber, which is connected to the pressure sensor, for any blockages or debris that may hinder the sensor’s ability to accurately detect the water level. Clear any obstructions to ensure proper functioning.
- Inspect the sensor hose for any pinholes or damage that could affect the pressure reading. If any pinholes are found, replace the sensor hose to ensure accurate measurements.
- Check and replace the pressure sensor with a new one to resolve the error.
- If the error still occurs despite taking the above steps, consider replacing the main board. A malfunctioning main board can affect the communication and functionality of the pressure sensor, leading to an error code.
F24: Overflow Error (Same as F02)
The F24 error code indicates an overflow error. This occurs when the overflow contact on the pressure switch remains closed for more than 60 seconds, resulting in an overflow error in the washing machine.
Solutions:
- Check the drain hose and ensure it is not plugged or kinked. A blocked or kinked drain hose can prevent proper water drainage, leading to an overflow. Clear any obstructions or straighten any kinks in the hose to ensure smooth water flow.
- Check the wire harness connections to the drain pump, pressure switch, and main board. Ensure that all connections are securely in place and that there are no loose or damaged wires. Faulty connections can disrupt the proper functioning of these components and contribute to the overflow error.
- Locate and clean the drain pump filter of any foreign objects or debris that may be obstructing water flow. A clogged filter can impede proper drainage and lead to an overflow situation.
- Test the drain pump to ensure it is functioning correctly. If the pump is faulty or not working properly, it may need to be replaced to resolve the overflow error.
- Verify that the inlet valve is shutting off the water properly. A stuck-open inlet valve can cause excessive water to enter the washing machine, leading to an overflow. If the valve is not shutting off as it should, it may need to be replaced.
- Check the air chamber and clear any obstructions to ensure proper functioning.
- Inspect the sensor hose for any pinholes and replace it if necessary.
- Test the pressure switch for proper operation. Ensure that the pressure switch is functioning as intended, or replace it if necessary.
UNB: Unbalance Error
The UNB error code occurs when there is an unbalance in the drum during the washing cycle. This usually happens when there is too little laundry in the drum, preventing it from spinning properly. As a protective measure, the appliance will display the “Unb” error at the end of the program.
Solutions:
- If there is too little laundry in the drum, it can result in an unbalanced load. Add more clothes to achieve a balanced load, ensuring that there is an adequate amount of laundry for proper spinning.
- Check if the washing machine is level and properly positioned. Uneven placement or a tilted appliance can contribute to an unbalanced load. Adjust the machine’s position to ensure it is stable and level on the floor.
- Ensure that the laundry is evenly distributed within the drum. If clothes gather on one side of the drum, it can cause an unbalanced load. Rearrange the laundry to evenly distribute the weight and prevent any heavy or bulky items from accumulating on one side.
- Remove any non-distributable items from the drum, such as large or heavy objects that cannot be evenly distributed. These items can disrupt the balance of the load and cause an unbalanced error.
Conclusion:
By being proactive in understanding and addressing common Hisense washing machine error codes like F01, F02, F03, F04, F05, F06, F07, F13, F15, F17, F18, F22, F23, and UNB, you can effectively diagnose and address the underlying causes. Whether it’s related to the water inlet, drain, heating, motor, sensor, or other components, following the recommended steps can help restore the functionality of your Hisense washing machine.
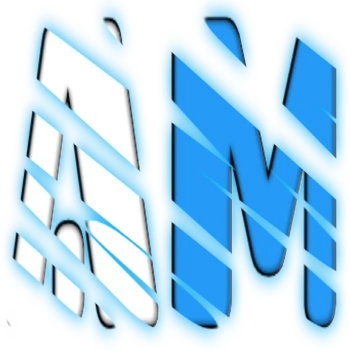
I am a master Appliance Repair technician with over 35 years of experience in the field. I am passionate about helping people troubleshoot their appliances and fix common problems. My website, appliancemode.com, provides a wealth of information on troubleshooting common appliance issues and deciphering error codes. This website aims to empower people to tackle appliance repairs themselves and save money on service calls.
What is f10
Water level sensor error
What is the problem of the machine constantly lets water in when it is supposed to spin?
Possible Causes:
Faulty Water Inlet Valve:
This valve controls the flow of water into the washing machine. If it’s not closing properly, water can continue to enter even during the spin cycle.
Bad Control Board:
The control board is the “brain” of the washing machine. It sends signals to various components, including the water inlet valve. A faulty control board might send incorrect signals, causing the valve to remain open during the spin cycle.