This guide will walk you through the most common error codes on Midea top load washers, explain what they mean, and provide practical troubleshooting steps to help you get your machine back to tackling your laundry pile.
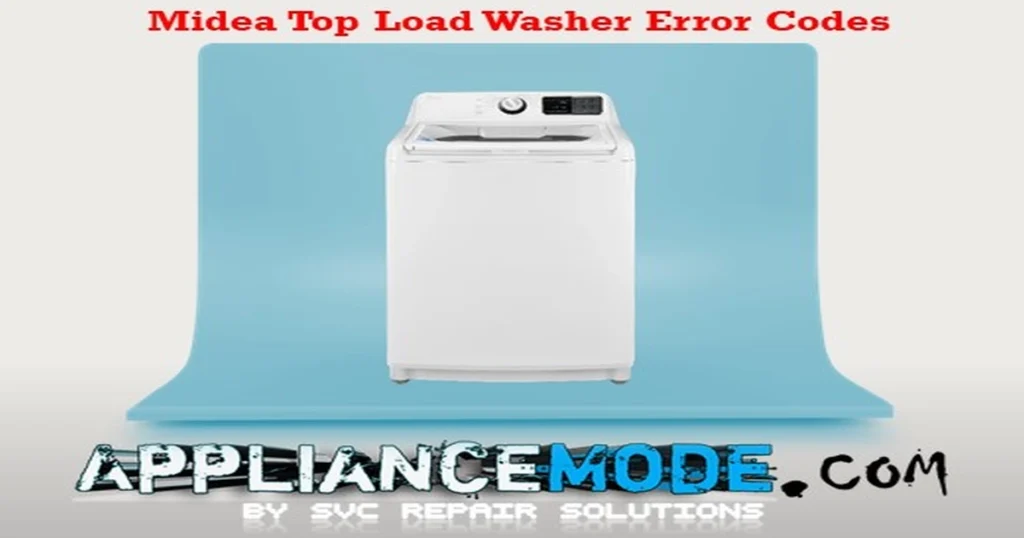
Important Safety Precaution: Always prioritize your safety. Before inspecting or attempting any repairs, unplug your Midea washer from the power outlet to prevent electric shock.
While some error codes can have different meanings across various Midea appliance types, this guide focuses specifically on the common codes encountered in Midea top load washing machines.
Understanding Midea Top Load Washer Error Codes
Here’s a breakdown of common error codes you might see on your Midea top load washer’s display:
E1: Inlet Valve Error
This code signals that your washer is having difficulty filling with water.
- Possible Causes:
- Closed or kinked water supply hoses.
- Insufficient water pressure.
- Clogged inlet valve filters.
- Faulty water inlet valve solenoid.
- Problem with the water level sensor.
- Issue with the main control board (PCB).
- Troubleshooting Steps:
- Check Water Supply: Ensure both hot and cold water faucets connected to the washer are fully open and that the hoses are not kinked or bent.
- Verify Water Pressure: Confirm that your household water pressure is adequate. Low water pressure can prevent the washer from filling correctly.
- Clean Inlet Valve Filters: Turn off the water supply and disconnect the hoses from the back of the washer. Inside the water inlet ports, you’ll find small filter screens. Carefully remove and clean any sediment or debris from these filters.
- Inspect Wire Harness: Check the wire harness connector for the water inlet valve for any loose or damaged connections.
- Test Inlet Valve Resistance: Using a multimeter, you can test the resistance of the water inlet valve solenoids. Refer to your washer’s service manual or reliable online resources for the expected resistance values (e.g., around 1650 Ω at 120Vac or 3600 Ω at 220Vac, but values can vary by model). Replace the valve if the resistance is outside the specified range.
- Check Water Level Sensor: A faulty water level sensor can also cause filling issues. While testing this component can be more complex, ensure its wire harness is connected properly.
- Main PCB: If the above steps don’t resolve the E1 error, the main PCB might be the issue, requiring professional diagnosis and potential replacement.
E2: Drain Pump Error
The E2 code indicates a problem with draining water from the washer.
- Possible Causes:
- Clogged drain hose or drain pump filter.
- Issue with the drain pump itself.
- Malfunctioning “retractor” (in models with this component).
- Faulty water level sensor.
- Problem with the main PCB.
- Troubleshooting Steps:
- Inspect Drain Hose: Ensure the drain hose is not kinked, bent, or clogged. Check the drain standpipe or sink drain for any obstructions.
- Clean Drain Pump Filter: Many Midea top load washers have a drain pump filter accessible from the front or back panel. Consult your manual for its location and how to clean it. Be prepared for some water to drain out when opening the filter.
- Check Drain Pump: If the hose and filter are clear, the drain pump might be faulty. In “up-drain” systems, this is a common culprit. You can often access the pump from the back or bottom of the washer.
- Test Drain Pump Resistance: Use a multimeter to check the resistance of the drain pump motor. Expected values can vary (e.g., around 16 Ω at 120Vac or 140 Ω at 220Vac), so consult your service manual if possible. Replace the pump if it doesn’t show the correct resistance or appears damaged.
- Examine Retractor: Some top load washers use a retractor mechanism to control draining and the shift between washing and spinning. If your model has a retractor and the washer isn’t draining, this component could be faulty. (Replacement typically requires accessing the bottom of the washer).
- Check Air Chamber: The air chamber is connected to the water level sensor by a hose. Ensure this hose is not blocked or kinked, as this can affect the sensor’s ability to detect the water level accurately, potentially leading to drain issues. (Cleaning the air chamber itself may require disassembling parts of the tub).
- Water Level Sensor: A malfunctioning water level sensor can also contribute to draining problems.
- Main PCB: If other components check out, the main PCB could be the source of the error.
E3: Lid Open Error
This code usually means the washer’s lid is not properly closed or detected as closed, preventing the cycle from starting or continuing for safety reasons.
- Possible Causes:
- Lid not fully closed.
- Obstruction preventing the lid from closing.
- Faulty lid switch assembly.
- Issue with the lid lock mechanism (if applicable and separate from the switch).
- Problem with the main PCB.
- Troubleshooting Steps:
- Ensure Lid is Closed: Make sure the lid is completely shut without any items or obstructions preventing it from sealing properly.
- Check Lid Switch Assembly: The lid switch is a safety mechanism that detects if the lid is closed. It can be part of the lid lock assembly or a separate switch. Inspect it for visible damage or misalignment.
- Test Lid Switch Continuity: If you have a multimeter, you can test the electrical continuity of the lid switch when the lid is open and closed. It should show continuity in one state and no continuity in the other, depending on its design.
- Inspect Lid Lock (and its Resistance): If your washer has a separate lid lock mechanism, ensure it’s engaging correctly. You can test the resistance of the lid lock solenoid if you can access it (expected resistance is often around 65 Ω, but verify with your manual).
- Main PCB: If the lid and switch/lock appear functional, the main PCB may be misinterpreting the signal.
E4 and/or E5: Spin Unbalance Error
This code indicates that the laundry load is unevenly distributed, causing excessive vibration during the spin cycle. This is a safety feature to prevent damage to the machine.
- Possible Causes:
- Unevenly distributed laundry.
- Washing a single bulky item.
- Washer not level.
- Problem with the suspension assembly.
- Issue with the balance ring on the wash drum.
- Faulty safety/impact switch bar.
- Troubleshooting Steps:
- Redistribute Laundry: Open the lid and manually redistribute the clothes inside the drum to create a balanced load. Avoid washing a single large, bulky item if possible, or add a few smaller items to help balance it.
- Level the Washer: Ensure the washing machine is placed on a level surface and all four leveling legs are making firm contact with the floor. Adjust the legs as needed.
- Check Suspension Assembly: The suspension rods help to cushion the wash drum during the spin cycle. If one or more rods are worn or damaged, it can lead to unbalance errors. Inspect the suspension assembly and replace if necessary.
- Inspect Balance Ring: The balance ring (often filled with a liquid) around the top of the wash drum helps to stabilize it during the spin. While less common, a damaged balance ring can cause unbalance issues.
- Safety/Impact Switch Bar: This switch detects excessive movement or vibration. Check for any deformation of the bar and test its continuity with a multimeter. It should show different continuity readings depending on whether it’s in its normal position or engaged by vibration.
F2 and/or C9: EEPROM Error
This code suggests a problem with the washer’s EEPROM (Electrically Erasable Programmable Read-Only Memory), which stores program and setting information.
- Possible Causes:
- Corruption of data in the EEPROM.
- Issue with the main control board (PCB).
- Troubleshooting Steps:
- Reset the Washer: Unplug the washer for at least 5-10 minutes to attempt to clear the error and allow the system to reset.
- Main PCB: If the error persists, it likely indicates a problem with the main PCB itself, which may require replacement.
F3: Water Level Sensor Error
The F3 code specifically points to a malfunction with the water level sensor, which is crucial for the washer to determine the correct water fill amount.
- Possible Causes:
- Faulty water level sensor.
- Kinked or blocked hose between the sensor and the air chamber.
- Clogged air chamber.
- Problem with the wire connection to the sensor or main PCB.
- Issue with the main PCB.
- Troubleshooting Steps:
- Check Sensor Hose: Inspect the rubber hose connecting the water level sensor to the wash tub’s air chamber for kinks, blockages, or leaks. Ensure it’s securely connected at both ends.
- Clean Air Chamber: The air chamber is a small cavity that traps air as water fills the tub, and the pressure change is read by the sensor via the hose. Sediment or debris can clog the air chamber, affecting the sensor’s reading. (Cleaning the air chamber may require some disassembly).
- Check Wire Connection: Verify the wire harness connection to the water level sensor and the main PCB.
- Test Water Level Sensor: Testing the water level sensor typically involves checking for specific capacitance or resistance values at different pressure levels. This often requires a multimeter capable of measuring capacitance and knowledge of the expected values for your specific sensor (e.g., capacitance between certain terminals around 40-50 nF, resistance between others around 20-40 Ω, but these values are examples and can vary).
- Main PCB: If the sensor and hose appear fine, the main PCB might be misinterpreting the sensor’s signal.
CL: Child/Control Lock Notification
This is not an error code indicating a malfunction but rather a notification that the control panel is locked, preventing accidental operation.
- Meaning: The Child Lock or Control Lock feature is activated.
- Solution: To deactivate the child lock, typically press and hold the “Soil Level” and “Temp” buttons simultaneously for about 3 seconds until the “CL” indicator disappears. (Button combinations may vary slightly by model, consult your user manual).
C8: Communication Failure between User Interface and Main Boards
This code signifies a loss of communication between the control panel (user interface) and the main control board.
- Possible Causes:
- Loose or damaged wire harness connecting the two boards.
- Faulty user interface board.
- Faulty main control board.
- Troubleshooting Steps:
- Inspect Wire Harness: Carefully check the wire harness and connectors that link the user interface board (behind the control panel) and the main PCB for any disconnections, damage, or corrosion. Ensure connections are secure.
- Test User Interface Board: Diagnosing a faulty user interface board often involves checking for proper voltage supply and signal output, which can require technical knowledge and a multimeter.
- Main Control Board: If the wiring is intact and the user interface board seems functional, the main PCB might be the source of the communication error.
FD: Lid Lock Error
The FD error code specifically points to a problem with the lid lock mechanism, which is essential for the washer to operate safely, especially during the spin cycle.
- Possible Causes:
- Faulty lid lock assembly.
- Obstruction preventing the lid lock from engaging.
- Issue with the wiring to the lid lock.
- Problem with the main PCB.
- Troubleshooting Steps:
- Check for Obstructions: Ensure nothing is blocking the lid lock mechanism from engaging properly when the lid is closed.
- Inspect Lid Lock Assembly: Examine the lid lock assembly for any visible damage or misalignment.
- Test Lid Lock Resistance: Using a multimeter, you can measure the resistance of the lid lock solenoid. Compare the reading to the expected value for your model (often around 65 Ω, but verify with your service manual).
- Check Wiring: Inspect the wire harness connecting the lid lock to the main PCB for any loose or damaged wires.
- Main PCB: If the lid lock assembly and wiring appear fine, the main PCB may be failing to send the correct signal to the lock.
By understanding these common Midea top load washer error codes and their potential solutions, you’re better equipped to diagnose problems with your washing machine and potentially get it back to running smoothly.
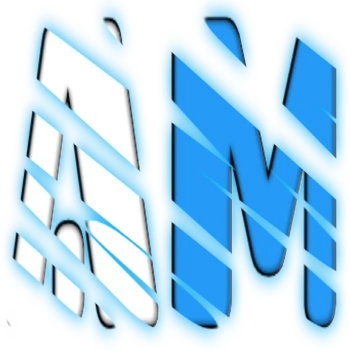
I am a master Appliance Repair technician with over 35 years of experience in the field. I am passionate about helping people troubleshoot their appliances and fix common problems. My website, appliancemode.com, provides a wealth of information on troubleshooting common appliance issues and deciphering error codes. This website aims to empower people to tackle appliance repairs themselves and save money on service calls.
Can I just say thank you!!!
E3 g CL would not go away on my midea top load washer. Just about every other site called for some type of disassembly. Press to buttons! You guys rock!!!
C8 error code