Understanding Midea Washing Machine Error Codes: A Comprehensive Troubleshooting Guide
This guide will help you to understand common Midea washing machine error codes and provide actionable troubleshooting steps.
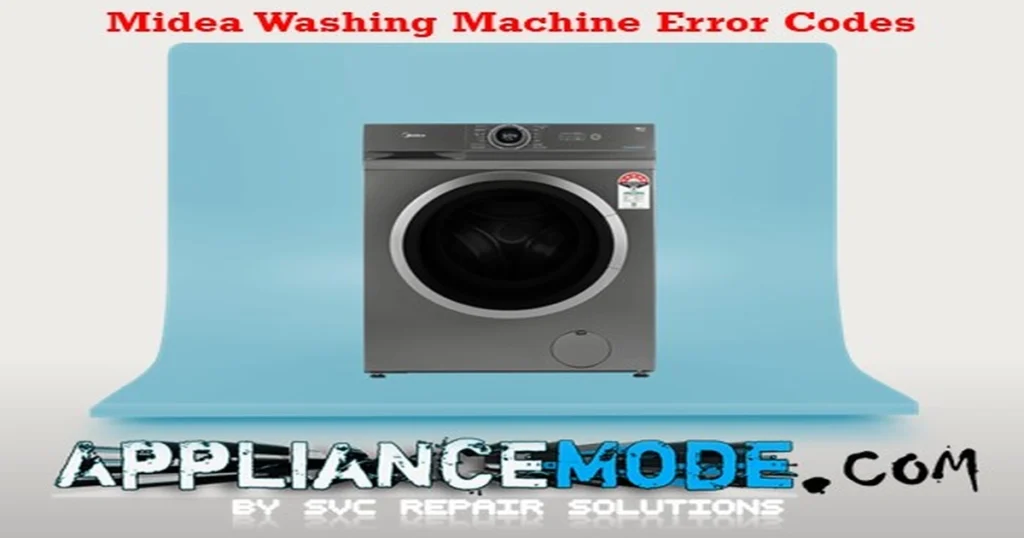
Important Safety Note: Before attempting any inspection or repair, ALWAYS unplug your Midea washing machine from the power outlet. Water and electricity are a dangerous combination. If you are uncomfortable working with electrical components or suspect a serious issue, it is always best to contact a qualified appliance repair technician.
Understanding Midea Washing Machine Error Codes
Midea washing machines use a system of alphanumeric codes to indicate specific faults or malfunctions. When an error occurs, a code will typically appear on the machine’s digital display. Each code corresponds to a particular area or component of the washing machine that requires attention.
Once you identify the error code, you can use this guide to understand the potential cause and follow the recommended troubleshooting steps.
Common Midea Washing Machine Error Codes and Troubleshooting
Here is a breakdown of common error codes you might encounter on your Midea washing machine:
E10: Water Inlet Valve Error
This error indicates that the washing machine is not filling with water correctly or within the expected time frame.
- Potential Causes:
- Closed or kinked water supply hose.
- Blocked inlet valve filter.
- Faulty water inlet valve.
- Problem with the water level sensor.
- Issue with the main control board (PCB).
- Wiring problems.
- Troubleshooting Steps:
- Check Water Supply: Ensure both the hot and cold water taps connected to the washing machine are fully open. Check the water supply hoses for any kinks, twists, or blockages.
- Clean Inlet Valve Filter: Turn off the water supply and disconnect the fill hoses from the back of the washing machine. You will find small filters inside the water inlet valve ports. Carefully remove and clean these filters under running water using a small brush. Reinstall the filters and hoses, ensuring a tight connection.
- Inspect Wire Harness: Check the wiring connection between the water inlet valve and the main PCB for any loose or damaged wires.
- Check Water Level Sensor: A faulty water level sensor can sometimes trigger an E10 error if it incorrectly reports the water level. (Further testing may require a multimeter and technical knowledge).
- Test/Replace Water Inlet Valve: If the above steps don’t resolve the issue, the water inlet valve itself may be faulty and require replacement.
E11, E12, E33: Water Level and Overflow Errors
These codes relate to issues with the washing machine’s water level detection and potential overflow situations.
- E11: Water Overflow Error: Indicates that the machine has detected an excessive amount of water in the drum.
- E12: Water Exceeds Level Error: Similar to E11, indicating the water level is too high.
- E33: Water Level Sensor Error: Points to a problem with the water level sensor itself.
- Potential Causes:
- Faulty water inlet valve (allowing water to enter continuously).
- Blocked or damaged pressure hose (connecting the drum to the water level sensor).
- Faulty air chamber (part of the water level sensing system).
- Faulty water level sensor.
- Issue with the main PCB.
- Troubleshooting Steps:
- Check Water Valve: If water continues to enter the drum even when the machine is off, the water inlet valve is likely stuck open and needs to be replaced.
- Inspect Pressure System: Examine the pressure hose and air chamber for any blockages, kinks, or leaks. Ensure the hose is securely connected to both the drum and the water level sensor.
- Check Water Level Sensor: The water level sensor may be faulty. You can sometimes test its resistance with a multimeter (refer to your service manual for specific values, but a typical Capacitance value between 1 and 2 = 2 and 3 might be around 45 nf and Ohmic Value between 1 and 3 around 25 Ω – Note: These values are examples and may vary by model.).
- Check Main PCB: If the sensor and pressure system appear fine, the issue could lie with the main control board.
E20, E21: Drain Pump Errors
These codes indicate a problem with the washing machine’s draining system.
- E20: Drain Pump Error: General error indicating a drainage issue.
- E21: Water Drainage Error: Specifically points to a failure in draining water.
- Potential Causes:
- Clogged drain hose.
- Blocked drain pump filter.
- Faulty drain pump.
- Issue with the main PCB.
- Troubleshooting Steps:
- Inspect Drain Hose: Check the drain hose for any kinks, twists, or blockages. Ensure it is not inserted too far into the drain pipe.
- Clean Drain Pump Filter: Most Midea washing machines have a drain pump filter accessible from the front lower panel. Place a towel down to catch water, then carefully unscrew and remove the filter. Clean it thoroughly of any lint, coins, or foreign objects.
- Check Drain Pump: The drain pump itself may be faulty. You can check the resistance of the drain pump coil with a multimeter. (Typical Ohmic Value might be around 30 Ω for 110V or 180 Ω for 220V – Note: These values are examples and may vary by model.). If the resistance is outside the expected range, the pump likely needs replacement.
- Check Main PCB: If the hose, filter, and pump appear functional, the main control board could be the source of the problem.
E30: Door Lock Error
This error signifies an issue with the washing machine’s door locking mechanism. The machine cannot start or complete a cycle if it doesn’t detect that the door is securely locked.
- Potential Causes:
- Door not closed properly.
- Obstruction preventing the door from closing or locking.
- Faulty door latch hook.
- Faulty door lock assembly.
- Issue with the main PCB.
- Troubleshooting Steps:
- Ensure Door is Closed Properly: Open and firmly close the washing machine door, ensuring nothing is caught in the door.
- Check Latch Hook: Inspect the plastic latch hook on the door for any damage or misalignment.
- Check Door Lock Assembly: The door lock assembly itself may be faulty. You can check its resistance with a multimeter (Typical Ohmic Value might be between 40 to 190 Ω – Note: This value is an example and may vary by model.). If it’s outside the range or appears physically damaged, it needs replacement.
- Check Main PCB: If the door and lock appear fine, the issue could be with the main control board.
E34, E35: NTC Sensor Errors
These errors relate to the NTC (Negative Temperature Coefficient) sensor, which monitors the water temperature in the drum.
- E34: NTC Sensor Open Error: Indicates an open circuit in the temperature sensor.
- E35: NTC Sensor Short Error: Indicates a short circuit in the temperature sensor.
- Potential Causes:
- Loose or damaged wiring to the NTC sensor.
- Faulty NTC sensor.
- Issue with the main PCB.
- Troubleshooting Steps:
- Check Wire Connection: Inspect the wiring connection between the NTC sensor (usually located near the heating element) and the main PCB for any loose or damaged wires.
- Check NTC Sensor Resistance: The resistance of the NTC sensor changes with temperature. You can test its resistance with a multimeter. (Typical Ohmic Value at 25°C/77°F might be around 4.6 kΩ – Note: This value is an example and may vary by model.). If the resistance is significantly different or shows an open/short circuit, the sensor needs replacement.
- Check Main PCB: If the wiring and sensor appear functional, the main control board could be the issue.
E36: Heater Assembly Error
This error indicates a problem with the water heating element. The machine has detected that the water temperature is not increasing as expected during a heating cycle.
- Potential Causes:
- Faulty heating element.
- Loose or damaged wiring to the heater.
- Faulty NTC sensor (providing incorrect temperature readings).
- Issue with the main PCB.
- Troubleshooting Steps:
- Check Wire Connection: Inspect the wiring connection between the heating element and the main PCB for any loose or damaged wires.
- Check Heater Resistance: You can test the resistance of the heating element with a multimeter. (Typical Ohmic Value might be around 16 Ω for 110V or 300 Ω for 220V – Note: These values are examples and may vary by model.). If the resistance is outside the expected range (usually a few dozen to a few hundred ohms depending on wattage and voltage), the heater may be faulty.
- Check NTC Sensor: A malfunctioning NTC sensor can also cause this error by providing incorrect temperature feedback. Test or replace the NTC sensor as described in the E34/E35 section.
- Replace Main PCB: If the heater and NTC sensor appear fine, the main control board could be the source of the problem.
E37, E38, E3A: Drying System Errors (for Washer-Dryer Models)
These codes specifically apply to Midea washer-dryer models and indicate issues with the drying function.
- E37: Drying-out NTC sensor error: Indicates an open or short circuit in the drying outlet thermistor.
- E38: Drying-in NTC sensor error: Indicates an open or short circuit in the drying inlet thermistor.
- E3A: Drying heater assembly error: Indicates a problem with the drying heating element or related components.
- Potential Causes:
- Loose or damaged wiring to the drying NTC sensors or drying heater.
- Faulty drying inlet or outlet NTC sensor.
- Faulty drying heating element.
- Tripped high-limit thermostat on the drying heater.
- Problem with the drying fan or its capacitor.
- Issue with the main PCB.
- Troubleshooting Steps:
- Check Wire Connections: Inspect the wiring connections to the drying NTC sensors, drying heater, and drying fan for any loose or damaged wires.
- Check Drying NTC Sensor Resistance: Test the resistance of the drying NTC sensors with a multimeter. (Typical Ohmic Value for the drying-out sensor at 50°C/122°F might be around 1.7 kΩ, and for the drying-in sensor at 90°C/194°F might be around 0.45 kΩ – Note: These values are examples and may vary by model.). Replace if the resistance is significantly off or shows an open/short circuit.
- Check Drying Heater: Test the resistance of the drying heating element. (Typical Ohmic Value might be around 18 Ω for 110V or 30 Ω for 220V – Note: These values are examples and may vary by model.). Check for continuity in the high-limit thermostat and reset it if tripped (usually a small button on the heater assembly).
- Check Drying Fan: Check if the drying fan is running. You can test the resistance between the common (C) and run (R) terminals (typical Ohmic value around 80 Ω) and between the common (C) and start (S) terminals (typical Ohmic value around 90 Ω) of the fan motor. (Note: These values are examples and may vary by model.). Also, check the drying fan capacitor (typical Capacitance value around 2.8 µF – Note: This value is an example and may vary by model.) for proper capacitance using a multimeter.
- Check Main PCB: If the above components appear fine, the main control board could be the issue.
E40: EEPROM Error
This error indicates a problem with the washing machine’s EEPROM (Electrically Erasable Programmable Read-Only Memory), which stores crucial program and settings data.
- Potential Causes:
- Data corruption in the EEPROM.
- Faulty main PCB.
- Troubleshooting Steps:
- Attempt a Reset: Sometimes, turning the machine off at the power outlet for a few minutes and then back on can clear temporary data issues.
- Replace Main PCB: If the error persists, the EEPROM is likely damaged, and the entire main control board will need to be replaced.
E50, E52, E53, E55, E56, E57, E58, E5A, E5B, E5C, E5D, E64: BLDC Motor and Inverter Board Errors
These codes are related to issues with the Brushless DC (BLDC) motor and its inverter control board, found in some Midea models.
- E50: BLDC motor inverter board error: General communication or internal fault with the inverter board.
- E52: Inverter board overload error: The inverter board has detected an overload condition on the motor.
- E53 or E58: IGBT temperature failure error: Indicates overheating of the IGBT (Insulated Gate Bipolar Transistor) modules on the inverter board.
- E55: BLDC motor speed signal loss error: The main PCB is not receiving a speed signal from the motor/inverter.
- E56: BLDC motor temperature failure error: The motor’s temperature sensor has detected overheating.
- E57: Inverter error: General error related to the inverter board operation.
- E5A: Lost connection between inverter and PCB error: Communication failure between the main control board and the inverter board.
- E5B or E5E: IGBT failure error: Indicates a failure within the IGBT modules on the inverter board.
- E5C: IGBT overvoltage error: The inverter board has detected an overvoltage condition.
- E5D: IGBT low voltage error: The inverter board has detected a low voltage condition.
- E64: Abnormal signal between inverter and main PCB error: Irregular communication signals between the main PCB and the inverter.
- Potential Causes:
- Loose or damaged wiring between the motor and the inverter board.
- Loose or damaged communication wiring between the main PCB and the inverter board.
- Faulty BLDC motor.
- Faulty inverter board.
- Issue with the main PCB.
- Overloaded drum.
- Troubleshooting Steps:
- Check Wire Connections: Inspect all wiring connections between the motor, inverter board, and main PCB for any looseness or damage.
- Check Motor Resistance: You can test the resistance between the coils of the BLDC motor (U, V, W). (Typical Ohmic Value between U and V = V and W = W and U might be around 5 Ω – Note: This value is an example and may vary by model.). Significant deviations can indicate a faulty motor.
- Check for Obstructions: Ensure the drum is not overloaded and can spin freely. Obstructions can cause motor stress.
- Check Inverter Board: The inverter board is complex. If wiring and motor resistance appear normal, the inverter board is likely faulty and requires replacement.
- Check Main PCB: In some cases, a faulty main PCB can cause communication errors with the inverter board.
E60, E61, E62: Universal Motor Errors
These codes are associated with washing machines that use a universal motor (a common type with carbon brushes).
- E60: Universal motor error: General error with the universal motor.
- E61: Abnormal motor speed signal error: The main PCB is receiving an irregular speed signal from the tachometer.
- E62: Motor TRIAC error: Indicates a problem with the TRIAC (Triode for Alternating Current) on the main PCB that controls motor speed.
- Potential Causes:
- Worn or damaged carbon brushes in the motor.
- Loose or damaged wiring to the motor or tachometer.
- Faulty tachometer (which measures motor speed).
- Tripped motor fuse protection.
- Faulty motor.
- Faulty main PCB (specifically the TRIAC).
- Troubleshooting Steps:
- Check Wire Connections: Inspect the wiring connections between the motor, tachometer, and main PCB for any looseness or damage.
- Check Carbon Brushes: On universal motors, carbon brushes can wear down over time. Locate and inspect the carbon brushes; replace them if they are significantly worn.
- Check Tachometer: The tachometer generates a voltage or pulse signal as the motor spins. You can test its output (requires spinning the motor and using a multimeter).
- Check Motor Fuse: Some models have a thermal fuse on the motor for protection. Check for continuity; if open, the motor may have overheated.
- Check Motor Resistance: You can test the resistance of the motor windings (requires a multimeter and knowledge of the motor’s terminals).
- Check Main PCB: If the motor and its components appear functional, the issue could be with the main control board, particularly the motor control circuitry (TRIAC).
E70: Shorted Button Error
This error indicates that the main control board has detected a short circuit on one or more buttons on the user interface (control panel).
- Potential Causes:
- Stuck or damaged button on the control panel.
- Moisture or debris on the control panel.
- Faulty user interface board.
- Issue with the main PCB.
- Troubleshooting Steps:
- Power Cycle: Turn the washing machine off at the power outlet for a few minutes, then plug it back in and turn it on. Sometimes, this can reset a temporary glitch.
- Clean Control Panel: Gently clean the control panel surface with a soft, dry cloth to remove any moisture or debris that might be affecting the buttons. Avoid using excessive moisture.
- Check for Stuck Buttons: Carefully inspect each button on the control panel to ensure none are physically stuck in the pressed position.
- Replace User Interface Board: If the error persists after cleaning and checking buttons, the user interface board itself may be faulty and require replacement.
- Replace Main PCB: In rare cases, a fault on the main PCB can cause this error.
E80, E81: Communication Failure Errors
These codes indicate a loss of communication between the user interface board (where the buttons and display are) and the main control board (the machine’s “brain”).
- E80: Communication failure between user interface board and main PCB: General communication breakdown.
- E81: Missing signal between UI and PCB: Specifically indicates that the main PCB is not receiving signals from the user interface.
- Potential Causes:
- Loose or damaged wire harness connecting the user interface board and the main PCB.
- Faulty user interface board.
- Faulty main PCB.
- Troubleshooting Steps:
- Check Wire Connection: Inspect the wire harness connecting the user interface board and the main PCB for any loose connectors or damaged wires. Ensure the connectors are securely plugged in.
- Check User Interface (UI) Board: The user interface board may be faulty and unable to communicate correctly. If the connection is secure, the UI board might need replacement.
- Check Main PCB: If the wire harness and user interface board appear functional, the main control board could be the source of the communication failure.
Midea Washing Machine Service Mode and Clearing Error Codes
Accessing the service mode can be helpful for diagnosing issues and clearing stored error codes.
How to Enter Service Mode:
- Ensure the washing machine drum is empty.
- Turn on the appliance.
- Press the following buttons sequentially: TEMP, SOIL, TEMP, SOIL. (Note: Button names may vary slightly depending on your model; consult your service manual if necessary).
Service Mode Functions (tO codes):
Once in service mode, the display may show various “tO” codes indicating different test functions:
- tO1: Displays the model version (e.g., 0##).
- tO2: Allows viewing and clearing stored error codes.
- tO3: Displays version information.
- tO4: Checks the display panel segments.
- tO5: Tests the drain pump.
- tO6: Checks the pressure sensor (water level sensor).
- tO7: Tests the main heater and NTC sensor.
- tO8: Tests the drying heater assembly (washer-dryer models).
- tO9: Initiates a wash phase test.
- t10: Initiates a spin phase test.
- t12: Tests the inlet valves.
How to Clear Error Codes:
Clearing stored error codes can sometimes resolve temporary glitches or is a necessary step after repairing a fault.
- Enter the service mode as described above.
- Navigate to the tO2 mode (this mode allows viewing error codes).
- Press the Start/Pause button. The display may show “Elt” or the last stored error code (e.g., “EXX”).
- To clear the last displayed error code (“EXX”), press and hold the SPIN and TEMP buttons simultaneously for approximately 3 seconds. You should hear a beep, and the display should change to “E00” to indicate the error has been deleted.
- You may need to repeat this process to clear multiple stored error codes.
- To exit service mode, turn off the appliance.
Conclusion
Midea washing machine error codes provide valuable clues about potential problems. By understanding the meaning behind these codes and following the troubleshooting steps outlined in this guide, you can often identify and resolve common issues yourself. Remember to prioritize safety by always unplugging the machine before inspection and repair.
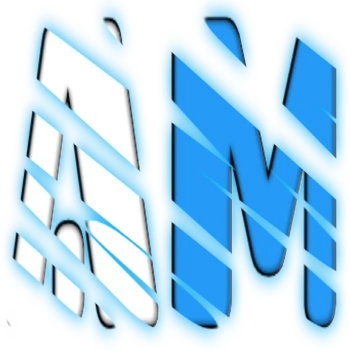
I am a master Appliance Repair technician with over 35 years of experience in the field. I am passionate about helping people troubleshoot their appliances and fix common problems. My website, appliancemode.com, provides a wealth of information on troubleshooting common appliance issues and deciphering error codes. This website aims to empower people to tackle appliance repairs themselves and save money on service calls.