Experiencing an error code on your Samsung dryer can bring your laundry routine to a frustrating halt. Those cryptic letters and numbers on the display can feel like a foreign language, leaving you wondering what went wrong and how to possibly fix it. The good news is that many Samsung dryer error codes point to common issues that you can often resolve yourself with a few simple troubleshooting steps.
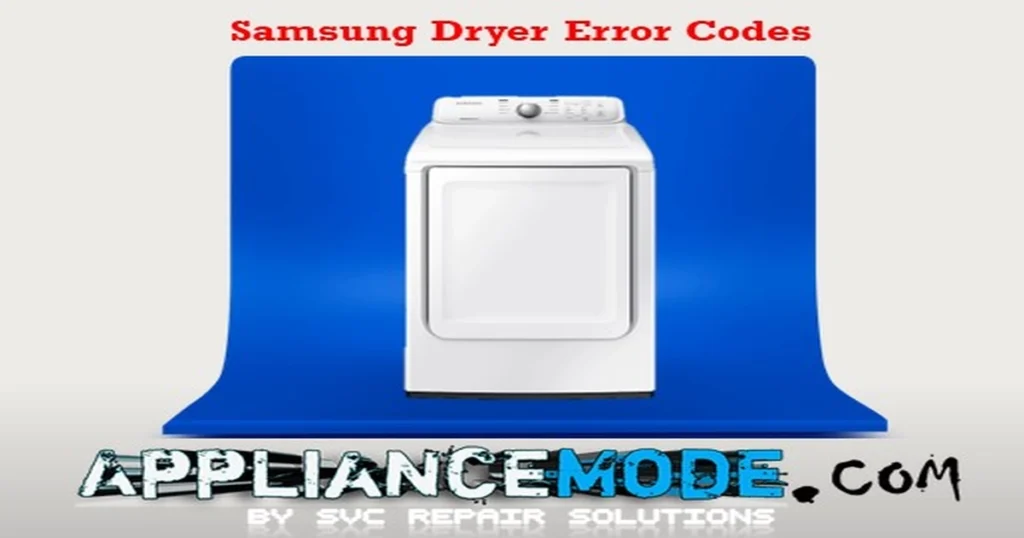
This guide is designed to help you understand what those error codes mean and empower you to tackle some of these problems, potentially saving you time and the cost of a service call.
Samsung Dryer Error Codes: Your Guide to Troubleshooting
Samsung dryers use specific error codes to indicate different problems. Identifying the code is the crucial first step in diagnosing the issue. Once you have the code, refer to the list below to understand its meaning and the possible causes and solutions.
Important Safety Note: Always unplug your dryer before attempting any inspection or repair. Exercise caution and if you are ever unsure about a step, it is best to consult a qualified appliance technician.
Here’s a breakdown of common Samsung dryer error codes:
Temperature and Heating Errors
These codes often relate to issues with the dryer’s heating system or temperature sensors (thermistors).
tC / tE / tC1: Thermistor 1 Error (Resistance too low or too high)
- Meaning: The main thermistor (Thermistor 1) which monitors the air temperature in the dryer drum is not reading correctly.
- Possible Causes: Clogged lint screen, restricted vent system, faulty thermistor, damaged thermistor wiring harness.
- Solutions:
- Clean the lint screen thoroughly before every load.
- Check and clear your dryer’s vent system for any blockages. A restricted vent is a very common cause of heating issues and error codes.
- Inspect the thermistor and its wiring harness for any visible damage.
- For advanced users: You can check the resistance of the vent thermistor 1 using a multimeter. At 25°C (77°F), the expected resistance is around 10 KΩ.
tC5: Thermistor 2 Error (Resistance too low or too high) – For Standard Vented Dryers
- Meaning: The secondary thermistor (Thermistor 2), often located in the exhaust, is reporting a resistance value outside the expected range.
- Possible Causes: Clogged lint screen, restricted vent system, faulty thermistor, damaged thermistor wiring harness.
- Solutions:
- Clean the lint screen.
- Check for restrictions in the vent system.
- Inspect the sensor bar resistance. (Note: The provided resistance values seem inconsistent and may require clarification from a service manual. A general check for cleanliness and intactness is recommended.)
- Check the vent thermistor 2 resistance. At 25°C (77°F), the expected resistance is around 240 KΩ.
- Check for a damaged or torn thermistor harness.
tC5: Compressor Temp Sensor Error – For Ventless or Heat Pump Dryers
- Meaning: The temperature sensor monitoring the compressor is reporting an issue.
- Possible Causes: The compressor thermistor resistance is out of range.
- Solutions:
- Check the compressor temperature sensor resistance. At 24°C (75°F), the expected resistance is around 50 KΩ.
- Check the thermistor voltage at the main control board (approximately 5 volts DC).
tC: Vent Sensor Error – For Ventless or Heat Pump Dryers
- Meaning: The thermistor in the vent system of a ventless or heat pump dryer has a resistance value outside the normal range.
- Possible Causes: Vent thermistor resistance is out of range.
- Solutions:
- Check the vent sensor resistance. At 26°C (79°F), the expected resistance is around 50 KΩ.
- Check the thermistor voltage at the main control board (approximately 5 volts DC).
- Clean the case filter (this may be specific to certain ventless models).
HC: Overheating Error – For Standard Vented Dryers
- Meaning: The dryer has detected an abnormally high temperature. This is a safety feature to prevent fires.
- Possible Causes: Invalid heating temperature during operation, thermistor resistance is out of range, clogged lint screen, restricted vent system.
- Solutions:
- Clean the lint screen thoroughly.
- Check and clear the vent system for any obstructions.
- Check the vent thermistor resistance (expected 10 KΩ at 25°C/77°F).
- Check for a damaged thermistor harness.
- Allow the dryer to cool down before attempting to run it again.
HC: Compressor Overheat – For Ventless or Heat Pump Dryers
- Meaning: The compressor in the heat pump system has overheated.
- Possible Causes: Dirty condenser coils, clogged evaporator coils, compressor temperature thermistor resistance is out of range, faulty DC fan motor, issue with the sealed refrigerant system.
- Solutions:
- Clean the evaporator and/or condenser coils. This often requires accessing internal components and may be best left to a technician.
- Check the compressor temperature sensor resistance (expected 50 KΩ at 24°C/75°F).
- Check the main PCB for the sensor pin voltage (approximately 5VDC).
- Check the DC fan motor condition and the main PCB for the fan pin voltage (expected 12 Vdc).
- Check the compressor winding resistance and capacitor.
- Issues with the sealed system (like Freon leakage or clogged capillaries) require a certified technician.
Motor and Drum Errors
These codes indicate problems with the dryer’s motor or the drum’s rotation.
3C / 3C1 / 3C2 / 3C3 / 3C4 / 3C5 / 3C6 / 3C7 / 3C8: BLDC Drum Motor Error
- Meaning: There is an issue with the Brushless DC (BLDC) drum motor or its control system.
- Possible Causes: Incorrect connections to the BLDC motor, faulty BLDC motor, faulty inverter board (controls the BLDC motor), faulty main control board, overloading the dryer.
- Solutions:
- Check all connector terminals and contacts on the motor and control boards for secure connections.
- Ensure the drum motor power cable and connector are properly connected.
- For advanced users: Check the BLDC motor resistance (expected 5 Ω between U, V, and W terminals).
- Reduce the size of the laundry load to prevent overloading (3C1 specifically relates to overloading).
- Check if the motor or the motor belt is damaged.
- If the inverter board or main board are faulty, they will need to be replaced.
Drainage Errors
This code is specific to ventless and heat pump dryer models that collect water.
5C: Overflow Error – For Ventless or Heat Pump Dryers
- Meaning: The dryer’s water collection system has detected an overflow.
- Possible Causes: Faulty wire harness, faulty float sensor (detects water level), faulty drain pump motor, clogged drain hose or filter.
- Solutions:
- Check the wire harness connectors related to the drainage system.
- Check if the float sensor circuit is open or shorted.
- For advanced users: Check the drain pump resistance (expected 370 Ω).
- Inspect and clear the drain hose and any accessible filters in the drainage system.
User Interface Errors
These codes relate to issues with the control panel or buttons.
bC2: Button Error
- Meaning: A button on the control panel is detected as being continuously pressed.
- Possible Causes: A stuck key, moisture or damage to the control panel.
- Solutions:
- Check if any buttons are physically stuck and try to gently free them.
- Inspect the user interface and/or control panel PCB (Printed Circuit Board) for any looseness, shorts, moisture, or visible damage. Ensure it is properly seated.
Door Errors
These codes indicate a problem with the dryer door or its sensor.
dC / dF: Door Open Error
- Meaning: The dryer’s control system detects that the door is open or not securely latched, preventing the cycle from starting or continuing.
- Possible Causes: The door is not fully closed, the door latch is not engaging correctly, the door switch is defective or loose, damaged door switch wiring harness.
- Solutions:
- Ensure the dryer door is completely closed and latched. Sometimes simply opening and firmly closing the door again can resolve this.
- Check the door and the door opening for any items of clothing or other obstructions preventing the door from closing properly.
- Check if the door switch is defective or loose.
- For advanced users: You can check the continuity of the door switch terminals with a multimeter.
- Door Open: Continuity between COM and NC, no continuity between COM and NO.
- Door Closed: No continuity between COM and NC, continuity between COM and NO.
- Check for a damaged or torn door switch wiring harness.
Power Supply Errors
These codes point to issues with the electrical power being supplied to the dryer.
FC: Power Frequency or Installation Fail Error
- Meaning: The dryer is detecting an invalid power source frequency or there is an electronic control problem related to voltage.
- Possible Causes: Invalid power source frequency (e.g., connecting the dryer to an incompatible power supply), electronic control board issue (invalid voltage reading).
- Solutions:
- Verify that the dryer is connected to a power source with the correct frequency (usually 50Hz or 60Hz depending on your region and the dryer’s specifications).
- For advanced users: Check the power frequency sensor circuit.
- Check the voltage at the dryer outlet using a multimeter.
- L1 and L2: ~240 Vac (60 Hz in North America)
- L1 and NEUTRAL: ~120 Vac (60 Hz in North America)
- L2 and NEUTRAL: ~120 Vac (60 Hz in North America)
- L1 and Ground: ~120 Vac (60 Hz in North America)
9C / 9E / 9C1 / 9E1 / 9C2: Invalid Power Source Error
- Meaning: The voltage supplied to the dryer is outside the acceptable range (specifically, the voltage between L1 and L2 is below 180 VAC for a sustained period).
- Possible Causes: Loose or incorrect power cord connection, issue with the household electrical supply, problem with the main control board connections.
- Solutions:
- Check the power cord connection at both the wall outlet and the terminal block on the back of the dryer. Ensure it is securely and correctly wired. If you are unsure, consult an electrician.
- Check the voltage at the terminal block on the dryer using a multimeter (L1 and L2 should be around 240 Vac, L1 and NEUTRAL/L2 and NEUTRAL should be around 120 Vac).
- Check the connectors at the Main PBA (main control board) to ensure the wire harness is securely connected.
Communication Errors
These codes indicate a failure in communication between different electronic components in the dryer.
AC / DF: Communication error between main board and control panel
- Meaning: The main control board is not communicating correctly with the control panel where you select cycles and options.
- Possible Causes: Damaged wiring harness between the boards, loose connections, faulty main control board, faulty control panel (sub-PCB).
- Solutions:
- Visually inspect the wiring harness connecting the main control board and the control panel for any signs of damage.
- Ensure the connector (often labeled CNC804) is properly seated on the main PCB.
- Ensure the connector (often labeled J3) is properly seated on the sub-PCB (control panel board).
- For advanced users: Measure the DC voltage going from the main PCB to the sub-PCB (expected 5VDC to 12VDC). If voltage is missing, test again with the connector removed. If still missing, the main PCB may be faulty.
- If the error persists after checking connections and voltage (if applicable), either the main PCB or the sub-PBA (control panel) may need to be replaced.
AC4: Communication error between main board and WIFI module
- Meaning: There is a problem with the communication between the main control board and the dryer’s WIFI module.
- Possible Causes: Faulty signals, incorrect or loose connector connections, faulty soldering on the WIFI module.
- Solutions:
- Carefully check the connector connections between the WIFI module and the main board for any looseness or incorrect placement.
- If comfortable, remove the WIFI module and inspect the soldering for any visible issues.
- Note: This error may only appear in a specific diagnostic mode (Line Test Mode) and might not indicate a functional problem during normal operation.
AC6: Communication error between main board and inverter board
- Meaning: The main control board is not communicating correctly with the inverter board that controls the drum motor.
- Possible Causes: Faulty signals, issues with wire connections or terminal contacts, faulty main board communication circuit, faulty inverter board communication circuit.
- Solutions:
- Check the wire connections and terminal contacts between the main and inverter PBAs for any disconnected or loose wires.
- If the communication circuits on either the main board or the inverter board are faulty, the respective board will need to be replaced.
Conclusion
Encountering an error code on your Samsung dryer can be disruptive, but by understanding what the codes signify and following these troubleshooting steps, you can often identify and resolve the underlying issue yourself. Start with the simple checks like cleaning the lint filter and ensuring clear vents, as these are frequent culprits. For more complex codes involving internal components or electrical measurements, the provided solutions can guide you, but remember to prioritize safety and disconnect the power.
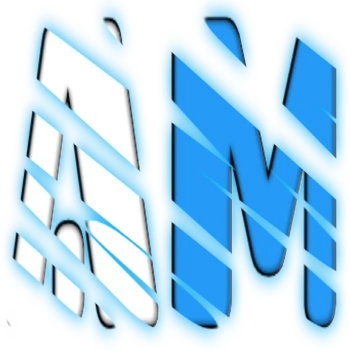
I am a master Appliance Repair technician with over 35 years of experience in the field. I am passionate about helping people troubleshoot their appliances and fix common problems. My website, appliancemode.com, provides a wealth of information on troubleshooting common appliance issues and deciphering error codes. This website aims to empower people to tackle appliance repairs themselves and save money on service calls.