To ensure the correct operation of the cooking function and basic safety items, the Smeg oven’s system constantly checks the feedback from the relays. The Checking Relay routine reads the available feedback and verifies the congruence between the relay status and the requested status.
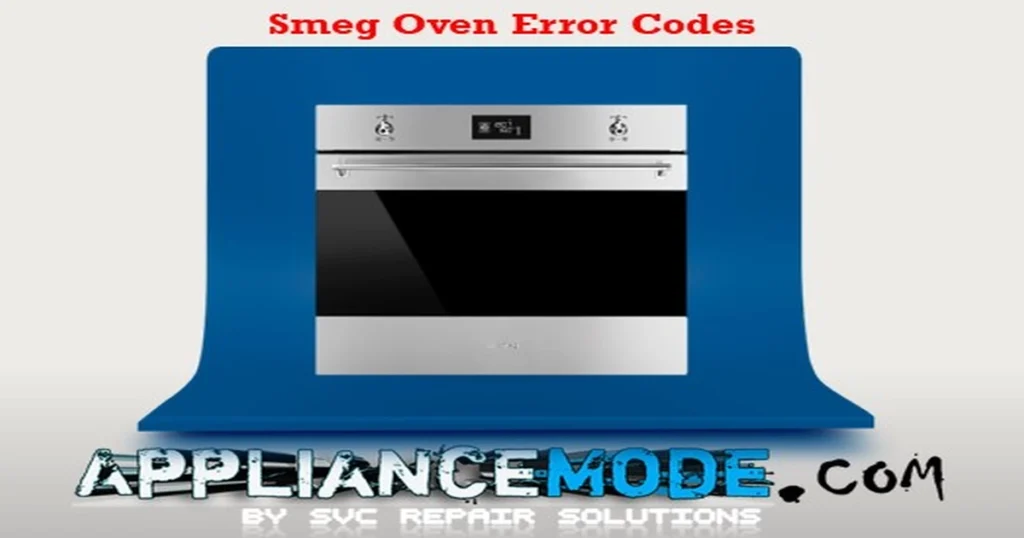
The outcome of this routine is taken into account during the oven cooking functions.
Smeg Oven Error Codes:
Before performing any maintenance or cleaning, always disconnect the appliance from the power supply.
Error 1: Oven probe error
The oven’s internal temperature probe has detected an abnormal temperature reading. This can happen for a few reasons:
- The probe is not inserted. Make sure the oven probe is properly inserted into its socket.
- Faulty probe: The probe itself may be damaged, reporting incorrect temperatures.
- Electrical issue: The probe’s connection to the oven’s electrical system might be faulty.
Solutions:
- Check the connection. Ensure the oven probe is securely plugged into its socket on the control board.
- If the probe appears loose, you may try carefully re-seating it. Do not force it.
- Replace the oven probe; it may have been damaged, and report abnormal temperatures to the board.
Error 2: High temperature error
This error indicates the oven has detected a temperature that exceeds safe operating limits. This could be due to several reasons:
- Faulty Temperature Sensor: The sensor might be malfunctioning and sending incorrect readings, causing the oven to overheat.
- Stuck Heating Element Relay: A relay on the control board might be stuck in the “on” position, continuously powering the heating element.
- Loose Connections: Faulty connections between the heating elements, temperature sensor, or control board can lead to erratic readings and overheating.
- Damaged Heating Element: A malfunctioning heating element could be drawing excessive power and causing overheating.
Solutions:
- Turn off the oven and unplug it. Let the oven cool down completely before attempting any troubleshooting.
- Basic Checks:
- Visually inspect the temperature sensor for any damage or improper placement.
- Check for loose or burned wires around the heating elements and control board.
- Advanced Troubleshooting:
- Using a multimeter (with proper electrical knowledge), check the continuity of the heating elements and ensure there are no short circuits.
- If you suspect a faulty relay or control board, replace it.
Error 4: Door lock error
This error indicates a problem with the oven’s door lock mechanism. The lock is designed to prevent accidental opening during high-temperature cleaning cycles (PYRO or PYRO ECO) for safety reasons.
When This Occurs:
- The door lock fails to engage during a PYRO or PYRO ECO function when the oven cavity temperature exceeds 300°C.
- The door lock activates unexpectedly during a standard cooking function (not a cleaning cycle).
Important Safety Precautions:
- Never force the door open. This could damage the lock mechanism or cause burns.
- Turn off the oven and unplug it from the power outlet. Let the oven cool down completely before attempting any troubleshooting.
Possible Causes:
- Faulty Door Lock: The door lock itself might be malfunctioning and not engaging properly.
- Electrical Issue: There could be a problem with the wiring or a faulty relay on the control board that’s causing the lock to activate unexpectedly.
Basic Troubleshooting (Before the Oven Cools Down):
- Visually inspect the door lock. Ensure there’s nothing obstructing the lock mechanism and that the door is properly closed.
Troubleshooting After the Oven Cools Down:
- Check connections: Verify all cables connected to the door lock and control board are secure and undamaged according to the wiring diagram.
- Reset the oven: Some Smeg models might have a reset function that can resolve temporary glitches. Consult your user manual for specific instructions.
Advanced Troubleshooting:
- Electrical testing: A qualified technician can use a multimeter to check the continuity of wires, diagnose short circuits, and test the door lock and control board functionality.
Error 5: Heater assembly error
This error indicates a problem with the oven’s round heating element. This can prevent functions that rely on this element, like baking and roasting, from working correctly.
Possible Causes:
- Faulty Heating Element: The element itself could be damaged and no longer heat properly.
- Loose Connections: The cables connecting the element to the main board might be loose or disconnected.
- Faulty Relay: A relay on the control board that controls the element might be malfunctioning.
Basic Troubleshooting:
- Visually inspect the heating element. Look for any visible damage, like cracks, burns, or discoloration.
- Check connections: Ensure all cables connected to the heating element and control board are secure and undamaged according to the wiring diagram.
Advanced Troubleshooting:
- Testing the Heating Element: Using a multimeter (with proper electrical knowledge), check the continuity of the heating element. If there’s no continuity, the element is likely faulty and needs replacement.
- Relay Issues: In some models, Error 5 can indicate a problem with the relay controlling the heating element.
- Models with Finder Relay: If your model uses a Finder relay for both round elements, Error 5 typically indicates a faulty relay that needs replacement.
- Models with Individual Relays: If your model uses separate relays for each round element, Error 5 might specify which relay (e.g., Relay 3) is malfunctioning. A qualified technician can diagnose and replace the faulty relay.
Error 6: Motor fan error
This error indicates a problem with the motor fan that circulates air inside your oven cavity. The fan is essential for even cooking and temperature control.
When This Occurs:
- The error appears when you try to use a function that requires the fan (e.g., baking or roasting).
- The oven will stop the function and display the error message.
Possible Causes:
- Faulty Motor Fan: The fan motor itself might be damaged and unable to operate.
- Loose Connections: The cables connecting the fan to the power board might be loose or disconnected.
- Faulty Relay: A relay on the control board that controls the fan might be malfunctioning.
Basic Troubleshooting:
- Listen for the fan: When you turn on the oven (assuming there is no error code), can you hear the fan running?
Advanced Troubleshooting:
- Check connections: Ensure all cables connected to the motor fan and control board are secure and undamaged according to the wiring diagram.
For qualified appliance repair technicians only:
- Electrical testing: A qualified technician can use a multimeter to check the continuity of wires, diagnose short circuits, and test the motor fan and control board functionality.
- Replacing components: If the issue is a faulty motor fan or relay, a qualified technician can replace them to restore proper function.
Error 7: Grill heater assembly error
This error indicates a problem with the grill heating element, which is used for broiling and browning food.
Possible Causes:
- Faulty Grill Heating Element: The element itself could be damaged and no longer heating properly.
- Loose Connections: The cables connecting the element to the control PCB might be loose or disconnected.
- Faulty Relay: A relay on the control board that controls the element might be malfunctioning.
Basic Troubleshooting:
- Visually inspect the grill heating element. Look for any visible damage, like cracks, burns, or discoloration.
- Check connections: Ensure all cables connected to the grill heating element and control board are secure and undamaged according to the wiring diagram.
Advanced Troubleshooting:
- Testing the Grill Heating Element: Using a multimeter (with proper electrical knowledge), check the continuity of the heating element. If there’s no continuity, the element is likely faulty and needs replacement.
- Relay Issues: A faulty relay controlling the grill element can also cause this error.
- The solution might involve replacing the control board.
Error 8: Tangential motor error
This error indicates a problem with the tangential fan motor. This fan helps cool down the oven cavity after cooking or during self-cleaning cycles (pyrolytic cleaning).
Possible Causes:
- Faulty Tangential Fan Motor: The motor itself might be damaged and unable to operate.
- Loose Connections: The cables connecting the fan motor to the power board might be loose or disconnected.
- Faulty Relay: A relay on the control board that controls the fan motor might be malfunctioning.
Basic Troubleshooting:
- Listen for the fan: After using the oven and allowing it to cool slightly, can you hear the tangential fan running?
Advanced Troubleshooting:
- Check connections: Ensure all cables connected to the tangential fan motor and control board are secure and undamaged according to the wiring diagram.
For qualified appliance repair technicians only:
- Electrical testing: A qualified technician can use a multimeter to check the continuity of wires, diagnose short circuits, and test the tangential fan motor and control board functionality.
- Replacing components: If the issue is a faulty tangential fan motor or relay, a qualified technician can replace them to restore proper function.
Error 9: Lower heater assembly error
This error indicates a problem with the lower heating element, also known as the hearth element. This element plays a crucial role in baking and roasting functions.
Possible Causes:
- Faulty Lower Heating Element: The element itself could be damaged and no longer heating properly.
- Loose Connections: The wire harness connecting the element to the power board might be loose or disconnected.
- Faulty Relay: A relay on the control board that controls the element might be malfunctioning.
Basic Troubleshooting:
- Visually inspect the lower heating element. Look for any visible damage, like cracks, burns, or discoloration.
Advanced Troubleshooting:
- Check connections: Ensure all cables connected to the lower heating element and control board are secure and undamaged according to the wiring diagram.
- Testing the Lower Heating Element: Using a multimeter (with proper electrical knowledge), check the continuity of the heating element. If there’s no continuity, the element is likely faulty and needs replacement.
- Relay Issues: A faulty relay controlling the lower element can also cause this error.
- The solution might involve replacing the control board.
Error E: WIFI module error
This error code indicates a problem with the Wi-Fi module, which allows you to connect your oven to your home network. This error will only be present on Smeg oven models equipped with a Wi-Fi connection board.
Possible Causes:
- Loose Connection: The cable connecting the Wi-Fi module to the main power board might be loose or disconnected.
- Software Glitch: A temporary issue with the oven’s software could be causing the Wi-Fi module to malfunction.
- Incorrect Programming: The oven’s master data might not be programmed correctly with the Wi-Fi module’s information.
- Faulty Flat Cable: The flat cable connecting the Wi-Fi module might be damaged.
- Faulty Wi-Fi Module: The Wi-Fi module itself might be malfunctioning.
Troubleshooting Steps:
- Check Connections: Ensure the cable between the Wi-Fi module and the power board is securely plugged in according to the wiring diagram.
- Restart the Oven: Sometimes a simple restart can resolve software glitches. Unplug the oven, wait a few minutes, then plug it back in and turn it on.
- Contact a Qualified Technician: If the above steps don’t resolve the issue, consult a qualified appliance repair technician. They can diagnose the problem and potentially replace the flat cable or Wi-Fi module if necessary.
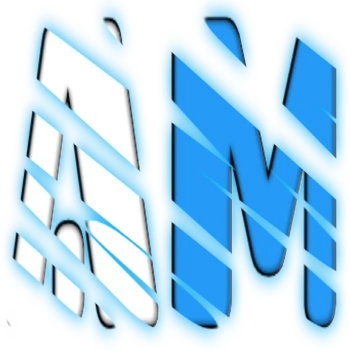
I am a master Appliance Repair technician with over 35 years of experience in the field. I am passionate about helping people troubleshoot their appliances and fix common problems. My website, appliancemode.com, provides a wealth of information on troubleshooting common appliance issues and deciphering error codes. This website aims to empower people to tackle appliance repairs themselves and save money on service calls.