Decode Your Dishwasher: A Comprehensive Guide to Whirlpool Error Codes
Your Whirlpool dishwasher is a modern marvel, but like any complex appliance, it can sometimes encounter hiccups. When it does, it speaks to you through a built-in communication system: error codes. These cryptic messages, often appearing as “FxEx” or simply “Fx,” might seem daunting at first glance. However, they are invaluable diagnostic tools, offering crucial insights into your appliance’s performance and health.

By understanding the language of these error codes, you gain the power to:
- Quickly and accurately pinpoint the root cause of a problem.
- Troubleshoot effectively, saving you time and hassle.
- Potentially avoid expensive repairs or unnecessary service calls.
This guide is your key to unlocking the secrets of your Whirlpool dishwasher’s error codes. We’ll provide a comprehensive resource for deciphering these messages, covering:
- Common Error Codes Explained: A clear breakdown of the most frequently encountered codes and what they signify.
- Practical Troubleshooting Steps: Actionable guidance on how to address issues based on the specific error code displayed.
Whether you’re greeted by a flashing “F8E1” or a persistent “F15,” this guide will empower you to understand and potentially resolve the issue, taking control of your dishwasher’s well-being.
Understanding Whirlpool Dishwasher Error Codes Formats: FxEx and Fx
Whirlpool dishwashers use two primary formats for their error codes: “FxEx” and “Fx”. While both indicate a problem, the “FxEx” codes often provide a more specific diagnosis, with ‘F’ indicating ‘Fault’, the first number (‘x’) typically indicating the system or component area (like fill, drain, heating), and the second number (‘Ex’) providing a more granular detail about the specific issue within that system. The simpler “Fx” codes also point to a system area but might be less specific in their diagnosis.
Important Safety Note: Before attempting any inspection or repair, ALWAYS unplug your dishwasher from the power source. Exercise extreme caution when dealing with electrical components and water. If you are uncomfortable performing any of the troubleshooting steps, it is always best to contact a qualified appliance repair technician.
Whirlpool Dishwasher Error Codes Beginning with “FxEx”
Here’s a breakdown of common “FxEx” error codes and their potential solutions:
F1E1: Pilot Relay Stuck Closed
- Meaning: The control board’s pilot relay, which controls a function (often related to the heating circuit), is stuck in the closed position (unable to open).
- Solutions:
- Inspect the wiring connected to the control board for any visible damage, frayed insulation, or signs of moisture.
- Repair or replace any damaged wires or connectors.
- Address any detected leaks on or near the control board.
- Carefully clean the control board using a suitable electronic cleaner (like PCB cleaner), ensuring it is completely dry before reconnecting power.
- If the error persists after these steps, the main control board may need replacement.
F1E2: Software Missing Error
- Meaning: Essential software components, such as the Appliance Personality Layer (APL) image or User Interface (UI) configuration code, are missing or corrupted on the main control board.
- Solutions:
- This typically requires replacing the main control board, as the software is integral to its function.
F2E1: Stuck Button in User Interface
- Meaning: One or more buttons on the dishwasher’s control panel are detected as being continuously pressed or stuck.
- Solutions:
- Visually inspect the buttons and surrounding plastic for any physical obstructions or damage. Replace the button assembly if necessary.
- Carefully open the console panel to access the user interface board. Check for any trapped wires or debris affecting the buttons.
- Examine the small micro-switches beneath the buttons on the user interface board for any signs of sticking.
- Check the wire connector between the user interface board and the main control board for a secure connection and any damage.
- If safe to do so and with the power disconnected, gently clean the user interface board using a suitable electronic cleaner.
- Replace any buttons that are physically stuck or not functioning correctly.
- Inspect and replace any damaged wiring harnesses.
- If the error continues, consider replacing the user interface board.
- If replacing the user interface board doesn’t resolve the issue, the problem might lie with the main control board.
F3E1: Thermistor Open Circuit
- Meaning: The dishwasher’s control unit is unable to get a valid temperature reading because the thermistor circuit (a temperature sensor) is open (broken connection). This prevents the control from accurately monitoring water temperature.
- Related Code: F3E2: Thermistor Short Circuit Error (Indicates excessive temperature readings due to a short circuit in the thermistor).
- Solutions:
- Ensure the thermistor’s connector is securely plugged into the control board and is clean and free of corrosion.
- Inspect the thermistor’s wiring for any damage and replace if necessary.
- Test the resistance of the NTC (Negative Temperature Coefficient) thermistor or OWI (Optical Wash Indicator) sensor using a multimeter. Compare the reading to the expected value (e.g., approximately 47.1 kΩ at 25°C / 77°F). If the reading is outside the specified range, the thermistor is likely faulty.
- If the issue persists after checking the thermistor and wiring, the main control board may be the culprit.
F3E3: OWI Calibration Failure (Same as F3E4: OWI Failure)
- Meaning: The Optical Wash Indicator (OWI) sensor, which detects water presence and turbidity (how dirty the water is), is present but either failed its calibration process or is not detecting water correctly.
- Solutions:
- Inspect the OWI sensor, usually located near the bottom of the tub, for any buildup of dirt, grime, limescale, or detergent residue.
- Thoroughly clean the OWI sensor. Advise on proper detergent usage and maintenance to prevent future buildup.
- Check the electrical connection between the OWI sensor and the main control board for security and damage.
- Inspect and replace any damaged wires in the OWI sensor harness.
- If cleaning and checking connections don’t resolve the error, the OWI sensor itself may need to be replaced.
- If replacing the OWI sensor doesn’t fix the problem, the main control board could be faulty.
F4E1: Communication Failure Between Wash Motor and Control Board
- Meaning: The main control board is not communicating correctly with the wash motor (the pump that circulates water through the spray arms).
- Related Codes:
- F4E2: Motor Communication Error (Similar to F4E1, general communication issue).
- F4E3: Wash Motor Not Functioning Error (Indicates the wash motor is not running when commanded).
- F4E4: Odra VSM Error (Specific error related to Variable Speed Motor (VSM) wash pumps).
- Solutions:
- Inspect the wiring harness and connectors between the wash motor and the main control board for any damage or loose connections.
- Look for signs of short circuits or other defects in the motor’s connectors or windings that could potentially damage the control board.
- If your model has a Variable Speed Motor (VSM), check the power and communication cables for the VSM board and replace any damaged wires.
- Ensure the holes in the spray arms are not blocked and the fine filter in the bottom of the tub is clean. (Blockages can strain the motor and affect operation).
- Measure the electrical resistance of the wash motor’s windings using a multimeter. Compare the reading to the specified values (e.g., ~52 Ω for VSM, ~8 Ω for single-phase main coil, ~11 Ω for single-phase AUX coil). Also, check the capacitance of single-phase wash pumps (~20 μF).
- If the measurements are outside the expected range or there is no continuity, the wash motor may need to be replaced.
- If the motor tests okay and connections are secure, the main control board might be the issue.
F5E1: Door Switch Stuck Open Error
- Meaning: The dishwasher’s control unit believes the door is continuously open, even when it is closed. This is usually due to a problem with the door latch or switch mechanism.
- Related Code: F5E2: Door Switch Stuck Closed Error (Indicates the control unit believes the door is continuously closed, even when it is open).
- Solutions:
- Visually inspect the door latch assembly for any physical damage, obstructions, or misalignment. Manually operate the latch to see if it moves freely.
- Ensure the door is fully closed and latched, then attempt to start a cycle.
- With the power disconnected, disconnect the door switch connector from the control board. Use a multimeter to measure the resistance across the door switch terminals. When the door is closed and latched, the reading should be close to 0 Ω (indicating continuity). If not, check the wiring harness for breaks or loose connections.
- If the switch doesn’t show continuity when the door is closed, replace the door switch assembly.
- If replacing the door switch doesn’t resolve the error, the main control board could be faulty.
F6E1: No Water Detected During Filling Cycle (Same as H2O error)
- Meaning: The dishwasher is attempting to fill with water but is not detecting that water is entering the tub.
- Related Code: F6E2: Fill Valve Malfunction Error (Indicates the control is not detecting current flow to the fill valve during filling, suggesting a faulty valve, wiring, or control).
- Solutions:
- Verify that the water supply tap to the dishwasher is fully open.
- Check the filter screen inside the end of the inlet hose that connects to the water tap for clogs. Clean it if necessary.
- Ensure the water pressure to your home is adequate for the dishwasher to fill properly.
- Inspect the electrical connections between the water inlet valve and the main control board, ensuring they are secure.
- With the power disconnected, unplug the inlet valve connector and measure the resistance across the valve terminals using a multimeter. Compare the reading to the specified value (e.g., ~3.8 kΩ at 220Vac, ~1.4 kΩ at 110Vac). If the reading is significantly different or shows an open circuit (OL), the valve may be faulty.
- Check the positioning of the drain hose. If it is installed too low, it can cause siphoning, where water drains out as it’s filling. Ensure the drain hose has a high loop or is connected to a standpipe at the correct height according to the installation instructions.
- If all other checks are satisfactory, the main control board may need replacement.
F6E3: Low Water or Suds Issue
- Meaning: The dishwasher is detecting either insufficient water levels or excessive suds, causing the wash pump to surge or cavitate (suck air).
- Solutions:
- Inspect the detergent dispenser for any issues, such as a missing gasket or blockage preventing proper detergent release.
- Check for excessive foam (suds) in the tub. Inquire about the type and amount of detergent and rinse aid being used. Using too much detergent, the wrong type of detergent (e.g., laundry detergent), or improperly adjusted rinse aid can cause excessive suds.
- Verify that the spray arms are not blocked and all the small holes are clear.
- Inspect the OWI (Optical Wash Indicator) sensor for dirt, calcium, or other deposits that might be interfering with its ability to detect water levels accurately. Clean the OWI if necessary.
- Ensure the dishwasher is properly loaded, as improper loading can sometimes affect water circulation and lead to low-water sensing.
F6E4: Overflow Error
- Meaning: The dishwasher’s overflow protection system has been activated. This typically involves a float switch in the drip tray at the bottom of the unit, which is triggered by water accumulating in the tray.
- Solutions:
- Check the drip tray located beneath the dishwasher for the presence of water. If water is found, there is a leak.
- Identify and address the source of the water leak. Common sources include faulty seals, hoses, pumps, or valves.
- Once the leak is repaired, remove all water from the drip tray.
- Inspect the float switch in the drip tray for any mechanical obstructions (like debris, screws, or a bent drip tray) that might be holding it in the “tripped” position. Remove any blockages.
- With the power disconnected, disconnect the float switch connector from the control board and test the microswitch using a multimeter for a short circuit.
- Check the wiring harness connection to the float switch for any damage or loose connections.
- If the float switch is mechanically free and the wiring is good, but the switch itself tests faulty, replace the float sensor assembly.
- If the issue persists after addressing leaks and checking the float switch, the main control board may need to be replaced.
F6E5: Fill Valve Stuck Open
- Meaning: The flow meter, which measures the amount of water entering the dishwasher, is detecting water flow even when the fill valve is supposed to be closed. This indicates the fill valve is not shutting off properly.
- Solutions:
- Close the water tap supplying the dishwasher.
- Try resetting the appliance (unplugging for a few minutes).
- Turn the appliance back on (but do not start a cycle). Re-open the water tap.
- Observe if water flows into the dishwasher without a cycle running. If water enters the tub with only the tap open and the machine idle, the inlet valve is faulty and needs replacement.
- If water does not flow in when the tap is opened with the machine idle, the main control board might be incorrectly energizing the fill valve and needs replacement.
F6E7: Flowmeter Malfunction Detected
- Meaning: Water is entering the dishwasher (detected by the overflow sensor or other means), but the flow meter is not generating pulses. The flow meter measures the volume of water by counting rotations of a small turbine. No pulses mean the meter isn’t working.
- Solutions:
- Inspect the electrical connection between the flow meter and the main control board for security and damage.
- During the water inlet cycle, visually confirm that the turbine inside the flow meter is spinning. If it’s not spinning, the flow meter assembly is likely faulty and needs replacement.
- With the power connected and during the fill cycle (use caution!), verify that the flow meter is receiving the correct voltage (typically +5 Vdc). If the correct voltage is not present, the main control board is likely the issue.
- Some flow meters can be tested using a magnet. Consult your service manual for the specific procedure.
- If the flow meter turbine is spinning and receiving the correct voltage, but still no pulses are detected by the control, the main control board may be faulty.
F6E8: Regeneration Valve Not Functioning
- Meaning: The regeneration valve, part of the water softening system in some models, is not operating correctly.
- Solutions:
- Inspect the electrical connections between the regeneration valve and the main control board, ensuring they are secure.
- With the power disconnected, unplug the regeneration valve connector and measure the resistance across the valve terminals using a multimeter. Compare the reading to the specified value (e.g., ~3.8 kΩ at 220Vac, ~1.4 kΩ at 110Vac). If the reading is significantly different or shows an open circuit (OL), the valve may be faulty.
- If the valve tests okay and connections are secure, the main control board might be the issue.
F7E1: Heater Relay Stuck Open Error
- Meaning: The relay on the control board that controls the heating element is stuck in the open position. This means power cannot reach the heating element, and the water will not heat up. This error might not be immediately visible to the user but is often detected during a service test cycle.
- Related Code: F7E2: Heating Element Stuck Closed Error (Indicates the heating element is receiving power continuously, even when it should be off, causing the temperature to rise unchecked).
- Solutions:
- Inspect the wiring harness connected to the heating element for any damage or loose connections.
- With the power disconnected, disconnect the heating element connector from the control board and measure the resistance of the heating element using a multimeter. Compare the reading to the expected value (e.g., ~26 Ω at 25°C / 77°F). Also, check the resistance of the thermal fuse and safety thermostat (Hi-limit) which should be very low (~0.1 – 1.2 Ω).
- With the power disconnected, disconnect the heating element connector and measure the resistance between the heating element coil and the dishwasher’s metal chassis (ground). The reading should be open (OL). If there is a reading indicating continuity, the heater is grounded, which can damage the control board.
- Check the resistance of the NTC/OWI thermistor (which monitors water temperature) to ensure it is within the expected range (e.g., ~17.2 kΩ at 50°C / 122°F). A faulty thermistor can sometimes cause heating errors.
- If the heating element and thermistor test okay and wiring is secure, the main control board is likely faulty and needs replacement.
F8E1: Slow or No Draining Error
- Meaning: The dishwasher is having difficulty draining water from the tub.
- Related Codes:
- F8E2: Drain Motor Not Functioning Error (Indicates the drain pump is not running).
- F8E3: Drain Motor Relay Stuck Closed (Indicates the drain pump is running continuously).
- Solutions:
- Check if the F6E5 (Fill Valve Stuck Open) error was previously stored. If so, resolve that issue first, as a continuous fill can overwhelm the drain system.
- Inspect the drain pump housing and the sump area at the bottom of the tub for any foreign objects (food particles, broken glass, small items) that might be blocking the impeller.
- Ensure the drain hose is correctly installed – it should have a high loop or be connected to a standpipe at the proper height to prevent siphoning. Check the drain hose for kinks or blockages. Verify that the connection to your home’s drain line (siphon) is clear and that any knockout plug in a new garbage disposal connection has been removed.
- Check for excessive suds, as high foam levels can impede draining. Review detergent usage as described in F6E3.
- Inspect the wiring harness connected to the drain pump for any damage or loose connections.
- With the power disconnected, measure the resistance of the drain pump motor using a multimeter. Compare the reading to the expected value (e.g., ~150 Ω at 220Vac, ~30 Ω at 120Vac for single phase; ~92 Ω for BLAC models).
- Check the connections between the OWI sensor and the control board, and inspect the OWI itself for dirt or deposits. While primarily for water sensing, a faulty OWI can sometimes indirectly affect drain cycles.
- Clean the holes in the spray arms and the fine filter in the tub, as blockages can affect overall water flow and drainage efficiency.
- If the drain pump tests okay, wiring is secure, and there are no physical blockages or siphoning issues, the main control board may need replacement.
F9E1: Diverter Position Sensor or Motor Error
- Meaning: In models with alternating wash functions (directing water to different spray arms at different times using a diverter valve), the control board cannot detect the correct position of the diverter motor.
- Related Codes:
- F9E2: Stuck Diverter Motor (Indicates the diverter is moving when it should be stationary, possibly due to a leak or faulty control).
- F9E3: Diverter Disk Failure (Indicates a problem with the physical disk within the diverter valve).
- Solutions:
- Check the wiring harness connected to the diverter motor and position sensor for any damage, breaks, or loose connections. Repair or replace wiring as necessary.
- With the power disconnected, measure the resistance of the diverter valve micromotor coil using a multimeter. Compare the reading to the expected value (e.g., ~6.4 kΩ at 220Vac, ~1.3 kΩ at 120Vac).
- Inspect the diverter valve assembly for any visible signs of water damage on the housing or around the electrical connectors, which could indicate a leak affecting the motor or sensor.
- Measure the resistance of the diverter position feedback circuit. As the diverter motor moves the valve, the resistance should change, often switching between open and short circuit depending on the position. Check for any connection issues in this circuit.
- With the power connected and during a cycle that should activate the diverter (use extreme caution!), measure the voltage on the feedback wire to ensure it is receiving the correct voltage (typically +5VDC). If not, the main control board may be faulty.
- Check the diverter valve for leaks and replace any seals if necessary. A leaky diverter can sometimes cause mechanical issues or damage electrical components.
- If all other components test okay and connections are secure, the main control board may need replacement.
F10E1: Dispenser Not Functioning Error (Same as FAE1 error)
- Meaning: The detergent and rinse aid dispenser assembly is not operating correctly.
- Solutions:
- Check the electrical connection between the dispenser assembly and the main control board for security and damage.
- With the power disconnected, measure the resistance of the dispenser coil (actuator) using an ohmmeter. Compare the reading to the expected value (e.g., ~7 kΩ at 220Vac, ~340 Ω at 120Vac). If the reading is significantly different or shows an open circuit, the dispenser assembly is likely faulty and needs replacement.
- If the dispenser coil tests okay and the wiring is secure, the main control board might be the issue.
F10E2: Vent Wax Motor is Not Functioning (Same as FAE2 error)
- Meaning: On models with an active vent drying system, the wax motor that opens and closes the drying vent is not operating correctly.
- Solutions:
- Check the wiring harness and connectors for the vent wax motor for any damage or loose connections.
- With the power disconnected, unplug the wax motor connector and measure its resistance using a multimeter. Compare the reading to the expected value (e.g., ~1-3 kΩ). If the reading is outside this range, the wax motor is likely faulty and needs replacement.
- If the wax motor tests okay and the wiring is secure, the main control board might be the issue.
F10E3: The Drying Fan Not Functioning (Same as FAE3 error)
- Meaning: The fan responsible for circulating air during the drying cycle is not operating.
- Solutions:
- Check the wiring harness and connectors for the drying fan for any damage or loose connections.
- With the power disconnected, unplug the fan connector and measure its resistance using a multimeter. Compare the reading to the expected value (e.g., ~250 Ω at 220Vac, ~150 KΩ at 13Vdc – note the difference in voltage and expected resistance for DC fans). If the reading is outside this range, the fan motor is likely faulty and needs replacement.
- If the fan tests okay and the wiring is secure, the main control board might be the issue.
Whirlpool Dishwasher Error Codes Beginning with “Fx”
These codes are generally less specific than the “FxEx” series but still point to a particular area of concern.
F1: Water Leakage Error
- Meaning: The dishwasher has detected water in the drip tray at the base of the unit, indicating a leak.
- Solutions:
- Verify the electrical connections for the float switch in the drip tray are secure.
- With the power disconnected, test the float switch’s microswitch using a multimeter to ensure it’s functioning correctly (should show continuity when lifted by water).
- If water is present in the drip tray, carefully inspect all hoses, connections, pumps, and the tub itself to locate the source of the leak. Replace any damaged components.
- Thoroughly dry the drip tray after fixing the leak.
- If the error persists despite no visible leaks and a functioning float switch, inspect and replace the main control board if necessary (though this is less common for a leak code).
F2: Water Inlet Valve Error
- Meaning: The dishwasher is having trouble filling with water, suggesting an issue with the water inlet system.
- Solutions:
- Ensure the main water supply tap to the dishwasher is fully open and that your home’s water pressure is within the acceptable range.
- Inspect and clean the filter screen located at the end of the inlet hose where it connects to the water tap.
- Clean the OWI (Optical Water Indicator) sensor at the bottom of the tub, as a dirty sensor can sometimes affect fill detection.
- Check the wiring harness connections to the water inlet valve for security and damage.
- With the power disconnected, measure the resistance of the inlet valve coil using a multimeter. Compare the reading to the specified value (e.g., ~3.8 kΩ at 220Vac).
- If the valve tests faulty, replace it. If the valve tests okay and connections are secure, inspect the main control board for defects.
F3: Draining Error
- Meaning: The dishwasher is not draining water properly or completely.
- Solutions:
- Inspect the drain hose for kinks, blockages, or improper positioning (ensure it has a high loop or is connected to a standpipe at the correct height to prevent siphoning).
- Clean the filter screen located in the drain pump housing at the bottom of the tub, removing any debris.
- Clean the OWI (Optical Water Indicator) sensor, as a dirty sensor can sometimes interfere with the drain cycle.
- Inspect the wiring and electrical connections of the drain pump for damage or looseness.
- With the power disconnected, test the resistance of the drain pump motor using an ohmmeter. Compare the reading to the expected value (e.g., ~150 – 210 Ω at 220 Vac for single phase; ~92 Ω for BLAC models).
- If the drain pump tests faulty, replace it. If the pump tests okay, wiring is secure, and there are no physical blockages or siphoning issues, check the main control board.
F4: NTC Sensor Error
- Meaning: There is an issue with the NTC (Negative Temperature Coefficient) thermistor, which is the sensor that measures water temperature.
- Solutions:
- Verify the incoming water temperature to your dishwasher is within the expected range.
- If the ambient temperature where the dishwasher is located is very low (e.g., below -2°C), the water might be too cold for the sensor to read correctly. Adding a small amount of warm water to the tub before starting the cycle can sometimes help in cold environments.
- Inspect the wiring and connectors for the thermistor (often part of the OWI sensor assembly) for any damage or loose connections.
- With the power disconnected, measure the resistance of the thermistor using an ohmmeter. Compare the reading to the specified value (e.g., approximately 465 Ω at 25°C). If the reading is significantly outside the range, the thermistor is faulty and likely requires replacing the OWI assembly it’s part of.
- If the thermistor tests okay and wiring is secure, inspect the main control board for defects.
F5: Pressure Switch Error
- Meaning: There’s a problem with the pressure switch or the air trap system it uses to sense water levels in the tub. (Note: Many newer Whirlpool models use the OWI sensor instead of a pressure switch for water level detection. This code is more common on older models.)
- Solutions:
- Inspect the small rubber or silicone tube connecting the air trap (a chamber in the sump area) to the pressure switch for kinks, blockages, or leaks.
- Check the air trap itself for blockages and clear any debris. Replace the air trap if it appears damaged.
- Check the wiring harness connected to the pressure switch for damage or loose connections.
- With the power disconnected, test the pressure switch using a multimeter to see if it’s operating correctly (continuity should change based on air pressure/water level). Replace the pressure switch if it’s faulty.
- If the pressure switch and related components test okay, inspect the main control board.
F6: Water Tap Closed Error
- Meaning: The dishwasher is not detecting incoming water flow, suggesting the water supply is off or restricted.
- Solutions:
- Ensure the water tap supplying the dishwasher is fully open and that you have adequate water pressure.
- Inspect and clean the filter screen at the end of the inlet hose.
- Clean the OWI (Optical Water Indicator) sensor.
- Check the wiring harness connection to the water inlet valve.
- With the power disconnected, measure the resistance of the inlet valve using a multimeter (e.g., ~3.8 kΩ at 220Vac). While this is an inlet valve check, this error primarily points to a lack of water getting to the valve.
F7: Water Liter Counter or Flowmeter Error
- Meaning: The flow meter, which measures the volume of water entering the dishwasher, is not functioning correctly.
- Solutions:
- Ensure the water tap is fully open and you have sufficient water pressure.
- Inspect and clean the filter screen at the end of the inlet hose.
- Clean the OWI sensor.
- Check the wiring harness connection to the flow meter.
- Inspect the flow meter itself for any visible damage or obstructions to the turbine. (Refer to F6E7 for more detailed flowmeter troubleshooting).
F8: Poor Heating Error
- Meaning: The dishwasher is not reaching the expected water temperature during the heating phase of the cycle.
- Solutions:
- Check for excessive suds in the tub, as excessive foam can sometimes interfere with heating efficiency. Review detergent usage as described in F6E3.
- Inspect the heating element for a buildup of limescale or mineral deposits, which can reduce heating effectiveness. Clean the heating element if necessary (vinegar or a commercial dishwasher cleaner can help).
- With the power disconnected, measure the resistance of the NTC thermistor using a multimeter (measures water temperature).
- With the power disconnected, measure the resistance of the heating element assembly (including the heater coil, thermal fuse, and safety thermostat) using an ohmmeter. Compare the readings to the expected values (e.g., Heater element ~26 Ω at 25°C; Thermal fuse/Safety thermostat ~0.1 – 1.2 Ω).
- If the heating element or thermistor test faulty, replace the component.
- If the heating element and thermistor test okay, the main control board might be faulty (specifically the heating relay).
F9: Software Failure
- Meaning: A general error related to the dishwasher’s internal software or programming.
- Solutions:
- This error typically indicates a problem with the main control board’s software or memory and usually requires replacing the main control board.
F10: Heater Relay “Stuck Open” Error
- Meaning: Similar to F7E1, this code indicates the relay on the main control board that controls the heating element is stuck in the open position, preventing the heater from receiving power.
- Solutions:
- Verify that the heating element cables are securely connected to the heating element and the control board.
- With the power disconnected, measure the resistance of the heating element assembly using an ohmmeter (including heater coil, thermal fuse, and safety thermostat). Compare readings to expected values (e.g., Heater element ~26 Ω at 25°C; Thermal fuse/Safety thermostat ~0.1 – 1.2 Ω).
- If the heating element assembly tests okay, the main control board is likely faulty (specifically the heating relay) and needs replacement.
F11: Wash Pump Error
- Meaning: There is a problem with the wash pump, which circulates water through the spray arms.
- Solutions:
- Inspect the wiring and connectors for the wash pump for any damage or loose connections.
- With the power disconnected, measure the resistance of the wash pump motor using a multimeter. Compare the reading to the expected value (e.g., ~52 Ω for VSM models).
- If the wash pump tests faulty, replace it. If the pump tests okay and wiring is secure, the main control board may be the issue.
F12: Missing Communication Between Main and Display Boards
- Meaning: The main control board and the user interface (display) board are not communicating with each other.
- Solutions:
- Check the ribbon cable or wire harness connecting the main control board to the user interface board for secure connections and any signs of damage. Reconnect or replace the cable if necessary.
- If the cable is secure and undamaged, consider replacing the user interface board, as it might be the source of the communication failure.
- If replacing the user interface board does not resolve the issue, the main control board may be faulty.
F13: EEPROM Error
- Meaning: An error related to the EEPROM (Electrically Erasable Programmable Read-Only Memory) on the main control board. This is where the dishwasher stores important operating parameters and settings.
- Solutions:
- This error typically indicates a fundamental problem with the main control board’s memory and usually requires replacing the main control board.
F15: Virtual Sensor Error
- Meaning: On some models, the control board uses “virtual sensors” that infer the presence or absence of water by monitoring the electrical current drawn by the wash pump and drain pump. Low current suggests an empty tub, while high current indicates water is present. This error occurs when these virtual sensor readings are inconsistent or unexpected.
- Solutions:
- Check your home’s water pressure, as low pressure can affect pump performance and potentially trigger this error.
- Inspect and test the wash pump and drain pump for proper operation and current draw. If either pump is drawing significantly more or less current than expected when running, it could indicate a problem with the pump itself.
- Replace the wash pump, drain pump, or main control board as necessary, based on the troubleshooting of the pumps and wiring.
Conclusion
Encountering an error code on your Whirlpool dishwasher can be frustrating, but by understanding what these codes mean and following systematic troubleshooting steps, you can often identify and resolve the issue yourself. This guide provides a valuable starting point for diagnosing common problems.
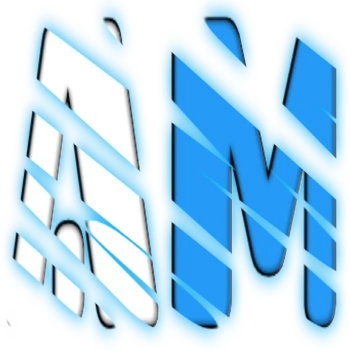
I am a master Appliance Repair technician with over 35 years of experience in the field. I am passionate about helping people troubleshoot their appliances and fix common problems. My website, appliancemode.com, provides a wealth of information on troubleshooting common appliance issues and deciphering error codes. This website aims to empower people to tackle appliance repairs themselves and save money on service calls.