Understanding Whirlpool Washing Machine Error Codes: Your Guide to Troubleshooting FxEx and Fx Errors
When your Whirlpool washing machine displays an error code, it’s like sending you a message in a language you might not understand. But don’t worry; this guide is here to help you decipher those codes and get your machine back on track.
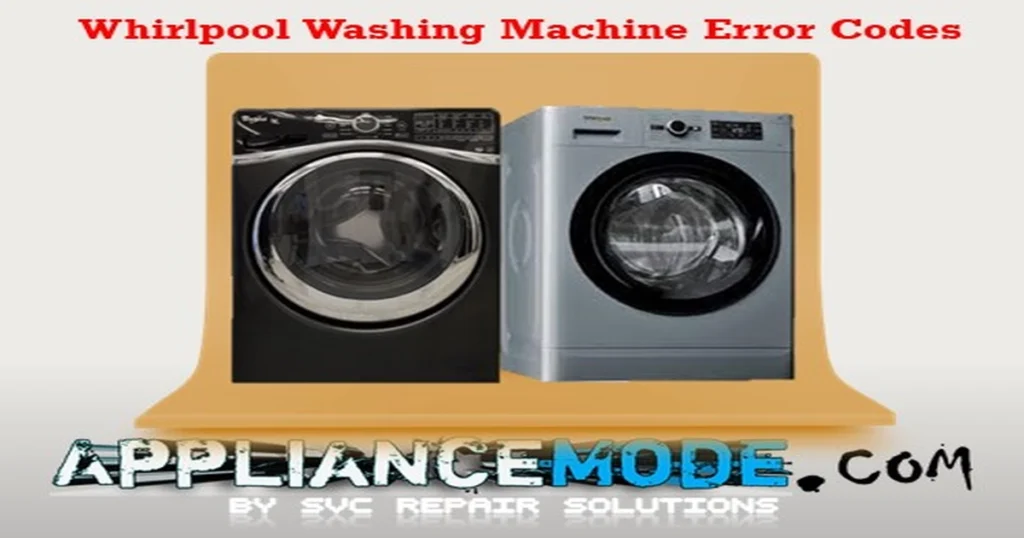
Understanding Whirlpool washing machine error codes can save you time and money on service calls. We’ll focus specifically on error codes that begin with “FxEx” and “Fx.” These codes provide valuable insights into potential issues affecting your washer’s performance.
Ready to become a Whirlpool washer error code expert? Let’s dive in!
Clearing Error Codes and Entering Service Mode on Your Washer
Before attempting any troubleshooting or repairs based on error codes, it’s often helpful to clear previous error codes and potentially enter service mode for diagnostics.
Important Safety Note: Always unplug the washer and exercise caution when attempting any troubleshooting or repairs.
Clearing Stored Error Codes:
- Ensure Standby Mode: Make sure the washer is in standby mode (plugged in but not running a cycle; all indicators should be off).
- Enter Service Mode: Press any three buttons (excluding Power) in a specific sequence within 8 seconds. Repeat this exact sequence two more times, for a total of three repetitions.
- Confirm Service Mode Entry: If successful, all indicators on the user interface will light up for 5 seconds, and “888” will appear in the estimated time remaining display. If there are no stored error codes, only the “888” display will remain.
- Hold Third Button to Clear: Once in service mode (“888” is displayed), press and hold the third button used in the entry sequence for 5 seconds.
- Confirm Clearing: If the codes have been successfully cleared, the display will revert to showing “888” without other indicators lit.
Exiting Service Diagnostic Mode:
- Turn Off the Washer: If your model has a power button, press it to turn off the washer. This usually terminates the service mode.
- Unplug the Washer: If turning off the washer doesn’t work, disconnect its power cord from the electrical outlet. This will force a reset and typically exit service mode.
Additional Information:
- Persistent Codes: If error codes reappear after clearing, it indicates an underlying issue that needs to be addressed.
Whirlpool Washing Machine Error Codes: FxEx Series
Here’s a breakdown of common Whirlpool washing machine error codes starting with “FxEx,” their explanations, potential causes, and troubleshooting steps.
Error Code | Explanation | Potential Causes | Solutions |
---|---|---|---|
F0E1 | Load in the drum during the “Clean Washer Cycle” warning. | Items left in the drum when the clean cycle was started. | Remove the load, clear the error code, and restart the “Clean Washer Cycle.” |
F0E2 | Over-suds warning. Washer detects excessive suds hindering draining/spinning. | Too much detergent used; not using HE detergent; reduced drainage system performance; clogged air chamber; kinked/leaking pressure sensor hose. | Measure water hardness and compare with detergent instructions; use recommended HE detergent; fix/reinstall drainage system (hose, siphon); remove/clean air chamber; check pressure sensor hose and housing for leaks and replace if needed. |
F0E4 | Water too hot error. Washer detects excessively hot water. | Cold water inlet hose connected to the hot water faucet; faulty NTC sensor; heater relay stuck closed (main board issue). | Double-check and switch cold/hot water hose connections; check NTC sensor resistance (should be ~9800 Ω at 86°F/30°C); check main board for stuck heater relay and replace if necessary. |
F0E5 | Unbalanced load warning. Washer detects an unusual imbalance. | Heavy items concentrated on one side; single or a few large pieces; potential main board issue. | Clear the error code; verify and redistribute the load (single large items are hard to balance); check and replace the main board if necessary. |
F1E1 | EEPROM error. Data integrity issue with the control board’s memory. | Discrepancy between retrieved data and stored checksum in EEPROM. | Disconnect power for 2 minutes, check outlet voltage, and reconnect; restart appliance; if error persists, replace the main board. |
F1E2 | Motor control unit undervoltage error. Motor control unit detects low mains voltage. | Low main voltage supply; faulty motor control board; faulty main board. | Check the main voltage supply; if error persists, replace the motor control board; if error still persists, replace the main board. |
F1E4 | Main relay stuck open or closed error. | Faulty main relay on the main board. | Replace the main board. |
F2E3 | Main board software not compatible with user interface error. | Faulty harness connection between UI and main board; corrupted firmware; faulty main board; faulty user interface. | Check the wire harness connection between the user interface and main board; replace the main board; if the error still occurs, replace the user interface. |
F3E1 | Water level sensor error. Also triggered by defective heater, drain pump, or related harness issues. | Blocked drain pump/filter/hose; blocked air chamber/pressure switch hose; faulty pressure switch/connections; defective heater/connections; defective drain pump/connections; main board issue. | Check drain pump/filter for foreign objects and clean; clean drain hose/siphon; check/clean air chamber/pressure switch hose; verify pressure switch condition and connections; check connections to heater/drain pump; check/replace main board. |
F3E2 | Wash NTC shorted or open. Water temperature sensor is out of range. | Faulty wiring/connections to NTC; defective NTC sensor; faulty main board. | Check wiring/connections between NTC and main board; check water NTC resistance (should be ~9800 Ω at 86°F/30°C); if error persists, replace the main board. |
F3E5 | Dry NTC shorted or open. Dry temperature sensor is out of range (washer-dryer). | Faulty wiring/connections to NTC; defective dry NTC sensor; faulty main board. | Check wiring/connections between NTC and main board; check dry NTC resistance (should be ~1480 Ω at 68°F/20°C); if error persists, replace the main board. |
F3E6 | Accelerometer error. | Faulty main board. | Replace the main board. |
F4E1 | Wash heater relay error. Main board cannot detect temperature rise from heater. | Faulty heater relay; incorrect connector plugging; defective harness; defective heater relay/main board. | Check heater relay function; ensure connectors are plugged correctly; check/replace harness; check/replace heater relay and/or main board. |
F4E2 | Heater error. Main control detects a heater circuit failure. | Faulty wiring/connectors to heater, main board, or pressure switch; grounded heater; damaged heater (contact with drum); water/corrosion at heater connector; pressure switch issue; control board issue. | Check/fix/replace wiring/connectors (especially for overheating/damage); check heater resistance to ground (replace heater if grounded); check heater resistance (~18-28 Ω); inspect heater for damage (check bearings, drum etc.); check heater connector for water/corrosion; verify pressure switch function; verify control board function. |
F4E4 | Dry fan motor error. Open or short circuit in the dry fan (washer-dryer). | Motor/fan wheel blockage; faulty wire harness connection; defective fan motor; faulty fan blade; control board issue. | Check motor/fan rotation for blockage; check wire harness connection; check fan motor resistance (~1800 Ω); check fan blade; check/replace the control board if necessary. |
F5E1 | Door switch error. | Door not closed properly; faulty wire harness connection; defective door switch contact; faulty main board. | Ensure the door is closed properly; check wire harness connection; check door switch contact resistance (OL open, ~0.1-1.0 Ω closed); check/replace the main board if necessary. |
F5E2 | Door lock error. Door fails to lock at cycle initiation. | Door not closed properly; mechanical problem with door lock system (door/hook); faulty harness between control board and door lock; door lock short circuit/water traces; door deformation; faulty harness connections (overload/damage); defective door lock solenoid; control board not supplying 120V to solenoid. | Ensure the door is closed properly; check/replace mechanical parts of the door lock system; check/replace harness between control board and door lock; check door lock for short circuit/water traces/deformation; check/replace wiring/connections; check door lock solenoid resistance (~80 Ω); enter service mode and check if the control board supplies power to the solenoid (replace door lock if yes, main board if no). |
F5E3 | Door unlock error. Control board fails to unlock the door within 240 seconds. | Mechanical issue (door lock, hook, hinge, door centering); main board unable to switch off the door lock. | After 5 minutes, push firmly on the door frame (if it unlocks, check/replace door lock, hook, hinge, and door centering); if the door locks when the appliance is off and the cancel/reset button is held in service mode (without pressing start), replace the main board. |
F5E4 “dr” | Door not open error. START pressed with door open, or after consecutive cycles without opening. | START button pressed while door is open; pre-set number of cycles completed without opening the door; control board unable to detect door switch opening/closing. | Resolve any underlying F5E1, F5E2, or F5E3 errors. Ensure the door is opened between cycles. |
F6E1 | Communication between control and motor control board errors (for models with external MCU). | Faulty harness/connections between control board and motor control unit; door switch contact issue; defective motor; faulty motor control unit; faulty main board. | Check harness/connections between control board and motor control unit; check door switch contact; check motor resistance (~8-22 Ω); check/replace motor control unit; check/replace main board. |
F6E2 | Communication between control board and user interface error. | Faulty harness/connections between control board and user interface unit; faulty user interface unit; faulty control board. | Clear the error code; check harness/connections between control board and user interface; check/replace user interface unit; check/replace control board. |
F6E3 | Communication between user interface and control board error. | Faulty harness/connections between user interface unit and control board; faulty user interface unit; faulty control board. | Clear the error code; check harness/connections between user interface and control board; check/replace user interface unit; check/replace control board. |
F7E1 | Drive Motor or Tachometer error. No or unreadable speed signal from tachometer. | No motor movement (motor defect, blocked, stalled, open harness); defective tachometer; open tachometer wiring; drum blockage; overload; high ambient temperature; damaged motor (bearings, fit, broken); activated thermal protector; faulty main board. | Check drum for blockage/noise/friction; check for overload/high ambient temp; check wire harness connections between motor and control board; check motor condition; check motor resistance (~8-22 Ω); check tachometer resistance (~115-170 Ω); check/replace main board. |
F8E0 | Steam inlet valve error. No water supply or steamer valve does not open (steam models). | Water tap closed; clogged water inlet filter; low water pressure; faulty harness connection between steamer control unit and steamer valve; faulty wiring; leaking hoses; faulty steamer control unit; defective steamer valve; faulty main board. | Check water tap/pressure; clean water inlet filter; check/fix/replace harness/wiring between steamer control unit and valve; check/fix/replace hoses for leaks; check steamer control unit function; check steamer valve resistance (~980 Ω); check/replace main board. |
F8E1 | Fill time out or inlet valve error. Washer not filling or main board not detecting water intake. | Water tap closed; disconnected/damaged/kinked inlet hose; clogged filters; improperly installed drain hose (siphoning); kinked/blocked/damaged pressure hose; faulty wiring/open circuit; defective water inlet valve; faulty control board. | Ensure water tap is fully open (both hot and cold if applicable); connect/check/install inlet hose properly; clean all filters; install drain hose correctly (prevent siphoning); check/clean/replace pressure hose; check wiring/connections; check water inlet valve resistance (~980 Ω); check/replace control board. |
F8E2 | Dispenser error. Dispenser motor unable to reach desired position. | Faulty wiring/open circuit; defective dispenser motor; dispenser switch not receiving +5Vdc; faulty main board. | Check wiring/connections; check dispenser motor resistance (~1580 Ω); check if dispenser switch receives +5Vdc (replace dispenser if yes, main board if no). |
F8E3 | Overflow error. Overflow contact on pressure switch closes. | Inlet valve not shutting off properly; clogged/kinked drain hose; clogged drain pump filter; faulty pressure switch (overflow contact stuck); air leakages in air chamber/pressure switch hose; short circuit in drain pump TRIAC; water leakages (internal hoses, dispenser, tub); overfoaming (too much detergent). | Check/replace inlet valve; check/clean drain hose/pump filter; check pressure switch function (including overflow contact); check/fix air chamber/pressure switch hose air leakages; check wiring between control board and float switch; check float switch for short circuits/water traces; clean drip tray and check for internal leakages (fix/replace); verify pressure switch function (replace aquastop switch if pressure switch is OK). |
F8E4 | Flowmeter error. | Defective inlet valve; faulty wiring between control board and flowmeter; flowmeter not receiving +5 volts; faulty main board. | Check/replace inlet valve; check wiring between control board and flowmeter; ensure flowmeter receives +5 volts (replace flowmeter if yes, main board if no). |
F9E1 | Drainage error. Water not properly removed despite pump function. | Excessive foam; air lock in outlet system; clogged outlet system (debris); water sensor malfunction (incorrectly detects water); siphon issue; clogged drain pump filter/hose; blocked equalization tank; blocked eco system/eco ball; electrical connections issue; drain pump resistance out of range; pressure switch contact issue; blocked air chamber/pressure hose; faulty main board. | Check/clean drain pump filter/hose/equalization tank; check eco system/ball; address excessive foam/air bubbles; check electrical connections between drain pump and control board; check drain pump resistance (~18 Ω); check pressure switch contacts; check/clean/replace air chamber/pressure hose; check/replace main board if necessary. |
Whirlpool Washing Machine Error Codes: Fx Series
Here’s a breakdown of common Whirlpool washing machine error codes starting with “Fx,” their explanations, potential causes, and troubleshooting steps.
Error Code | Explanation | Potential Causes | Solutions |
---|---|---|---|
F01 | Main board “main board TRIAC’s short or open circuit” error. | Water leaks causing electrical shorts; short circuits at the motor terminal board; issues with wash heating element connections/element; issues with pressure switch wiring/connectors; issues with dry heating element wiring/connectors; faulty main circuit board. | Inspect for water leaks and address; inspect motor terminal board for shorts; check wash heating element connections/element; check pressure switch wiring/connectors; disconnect appliance for 2 mins, check dry heating element wiring/connectors on main board; inspect/replace main circuit board. |
F02 | Motor error. | Water leaks causing electrical shorts; mechanically jammed/seized motor; issues with motor connector; incorrect motor winding resistance; incorrect tachometer resistance; issues with tachometer wiring; faulty motor; faulty main circuit board. | Inspect for water leaks and address; confirm motor is not jammed; inspect motor connector; measure motor winding resistance (~17 Ω for 3-phase); measure tachometer resistance (~115-170 Ω); inspect tachometer wiring; consider replacing motor; inspect/replace main circuit board. |
F03 | NTC short/open circuit error. Temperature sensor is not functioning correctly. | Issues with sensor wire harness connector; incorrect NTC sensor resistance; faulty NTC sensor; faulty main circuit board. | Inspect sensor wire harness connector; measure NTC sensor resistance (~20 KΩ at 20°C) and replace NTC if incorrect; if problem persists, inspect/replace main circuit board. |
F05 | Pressure switch error. | Issues with connector contacts between PCB and pressure switch; issues with drain pump connector; clogged pump filter, drain hose, or wall drain outlet; clogged air trap; pinholes in pressure hose; issues with pressure switches; faulty drain pump/linear pressure switch; faulty main PCB. | Inspect connector contacts (PCB to pressure switch); inspect drain pump connector; clean pump filter, drain hose, wall drain outlet; remove/clean air trap; inspect pressure hose for pinholes; check pressure switches; if problem persists, inspect/replace drain pump/linear pressure switch; if problem still persists, inspect/replace main PCB. |
F06 | Door lock error. | Water leaks causing electrical shorts; issues with door lock terminal wiring; issues with door lock assembly; faulty main circuit board. | Inspect for water leaks and address; inspect door lock terminal wiring; check door lock assembly with ohmmeter; if problem persists, inspect/replace main circuit board. |
F07 | Heating element error. | Contacts on heater assembly not properly connected to main board; incorrect wash heating element resistance; faulty heating element; faulty main board. | Verify heater assembly contacts are properly connected to main board; measure wash heating element resistance (~30 Ω) and replace if incorrect; if issue persists, inspect/replace main board. |
F08 | Heater relay stuck error. | Issues with heater assembly connections on main circuit board; electrical leakage between heater ends and ground; incorrect washing heating element resistance; faulty heating element; faulty main circuit board. | Inspect heater assembly connections on main circuit board; verify no electrical leakage between heater and ground; measure washing heating element resistance (~30 Ω) and replace if incorrect; if issue persists, check/replace main circuit board. |
F09 | EEPROM error. | Faulty main board; faulty user interface. | Check/replace main board if necessary; if problem still occurs, check/replace user interface. |
F11 | Drain pump error. | Issues with drain pump connections on main circuit board; clogged pump filter, drain hose, or wall drain outlet; incorrect pump resistance; faulty drain pump; faulty main circuit board. | Inspect drain pump connections on main circuit board; clean pump filter, drain hose, wall drain outlet; measure pump resistance (~190 Ω) and replace drain pump if incorrect; if issue persists, check/replace main circuit board. |
F12 | Communication error between main board and user interface error. | Issues with connector contacts between main board and user interface unit; faulty user interface; faulty main board. | Inspect connector contacts between main board and user interface; check/replace user interface if necessary; if problem still occurs, check/replace main board. |
F13 | Dry NTC sensor open/short-circuiting error (washer-dryer). | Blocked/clogged condenser filter; fluff/debris on blower fan; issues with NTC sensor connector contacts on main circuit board; incorrect NTC sensor value; faulty NTC sensor; faulty main circuit board. | Verify condenser filter is not blocked; inspect/clean blower fan; check NTC sensor connector contacts on main circuit board; measure dry NTC sensor value (~201 KΩ at 20°C) and replace NTC if incorrect; if issue persists, check/replace main circuit board. |
F15 | Dry heater element error (washer-dryer). | Issues with dry heating element connections on main circuit board; incorrect dry heating element resistance; electrical leakage between dry heater and ground; issues with drain pump wiring/resistance; issues with water inlet valve connections/wiring; faulty main circuit board. | Inspect dry heating element connections on main circuit board; measure dry heating element resistance (~26 Ω); verify no electrical leakage between dry heater and ground; check drain pump wiring and resistance; inspect water inlet valve connections/wiring; if issue persists, check/replace main circuit board. |
F18 | Communication error between main board and 3 phase motor. | Faulty main board. | Check/replace main board if necessary. |
F19 | Dry fan error (washer-dryer). | Issues with dry fan motor connections on main circuit board; incorrect dry heating element resistance (likely a typo in original, should be fan motor resistance); short/open circuits in fan motor; seized fan motor; faulty main circuit board. | Inspect dry fan motor connections on main circuit board; check dry fan motor resistance; check fan motor for short/open circuits; ensure fan motor turns freely; if necessary, check/replace main circuit board. |
Conclusion
Navigating Whirlpool washing machine error codes can seem daunting at first, but by understanding the meaning behind these FxEx and Fx codes and following the troubleshooting steps provided, you can often identify and resolve issues yourself. Remember to prioritize safety by always unplugging the appliance before inspecting components.
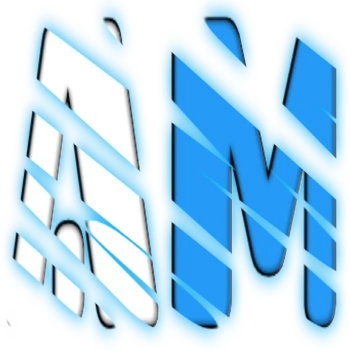
I am a master Appliance Repair technician with over 35 years of experience in the field. I am passionate about helping people troubleshoot their appliances and fix common problems. My website, appliancemode.com, provides a wealth of information on troubleshooting common appliance issues and deciphering error codes. This website aims to empower people to tackle appliance repairs themselves and save money on service calls.